ABSTRACT
The paper aims on the design, development and the fabrication of the robot which can dig the soil, put the seeds, leveler to close the mud and sprayer to spray water, these whole systems of the robot works with the battery and the solar power. More than 40% of the population in the world chooses agriculture as the primary occupation, in recent years the development of the autonomous vehicles in the agriculture has experienced increased interest.
The vehicle is controlled by Relay switch through IR sensor input. The language input allows a user to interact with the robot which is familiar to most of the people. The advantages of these robots are hands-free and fast data input operations. In the field of agricultural autonomous vehicle, a concept is been developed to investigate if multiple small autonomous machine could be more efficient than traditional large tractors and human forces. Keeping the above ideology in mind, a unit with the following feature is designed:
- Ploughing is one of the first steps in farming. During this process we till the land and make it ready for the seed sowing. By tilling we mean that a plough will be used which will have teeth’s like structure at the end and will be able to turn the top layer of soil down and vice-versa.
- Seed sowing comes next where the seeds need to be put in ground at regular intervals and these needs to be controlled automatically. Limiting the flow of seeds from the seeds chamber is typically doing this.
- Mud leveler is fitted to close the seeds to the soil and to level the ground.
- Water pump sprayer is used to spray the water).
SCOPE OF PROJECT
The Present project aims at designing an intelligent robotic vehicle which can be controlled wirelessly through RF communication.
The main aim for our project has been to develop a solar operated digging machine, which is solar powered. In this machine we used a solar panel to capture and convert solar energy into electrical energy which in turn is used to charge a 12V battery, which then gives the necessary power to a shunt wound DC motor. This power is then transmitted to the rear wheel through gear drives. In this project an attempt is made to make the electric and mechanical systems share their powers in an efficient way.
OBJECTIVES
The objective of this paper is to present the status of the current trends and implementation of Agricultural and autonomous systems and outline the potential for future applications. Different applications of autonomous vehicles in agriculture have been examined and compared with conventional systems, where three main groups of field operations have been identified to be the first potential practical applications: crop establishment, plant care and selective harvesting.
METHODOLOGY
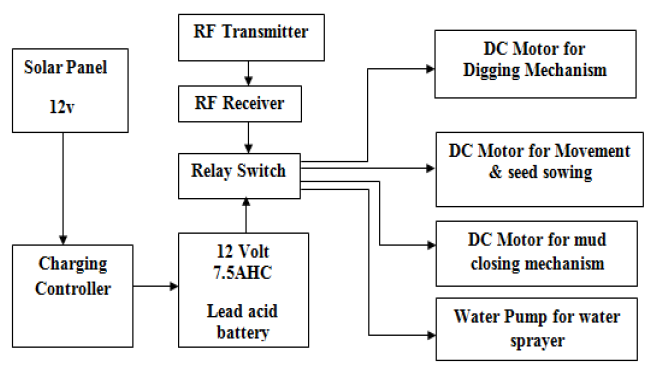
Fig: Block Diagram of Multi Purpose Agricultural Robot.
The basic aim of this project is to develop a multipurpose machine, which is used for digging the soil, seed sowing, and leveler to close the mud and water sprayer to spray water with least changes in accessories with minimum cost. This whole system of the robot works with the battery and the solar power.
OPERATIONS
Steering Operation
- Rack and pinion Mechanism for steering operation.
- The pinion is coupled with the DC Motor.
- The power for motor is regulated by Relay switch.
- The direction of motor rotation can be controlled by remote controller for steering the vehicle to either left or right side direction.
Cultivating Operation
- A DC Motor coupled with the screw rod is used.
- The power for motor is regulated by relay switch.
- The screw rod rotates and the nut welded to the cultivator slides between the screws of the screw rod.
Seed Sowing Operation
- A sheet metal hopper box is used for Seed storage.
- We have provided 3 holes to the main wheel shaft, where the Storage box is placed above it.
- The main wheels are powered by DC motor which is regulated by a Relay switch and is controlled by a remote controller.
- As the motor is switched on, the wheels tend to rotate and rotation of shaft makes the seeds fall on the cultivated filed.
Mud Closing and Leveling Operation
- A Sheet metal Plate is used as mud closer and leveler.
- The sliding mechanism is used for leveler up & down movement.
- The Leveler is powered by a DC motor which is regulated by Relay switch and controlled by a remote controller.
- As the leveling plate moves downward to the ground level, the mud is closed in the sowed soil.
Water Spraying Operation
- A water container is used for water storage.
- A water pump is used for pumping water to the water sprayer.
- The water flows to the sprayer through pipe.
- The power for pump is regulated by a toggle switch.
CONCLUSION
In agriculture, the opportunities for robot-enhanced productivity are immense – and the robots are appearing on farms in various guises and in increasing numbers. The other problems associated with autonomous farm equipment can probably be overcome with technology. This equipment may be in our future, but there are important reasons for thinking that it may not be just replacing the human driver with a computer. It may mean a rethinking of how crop production is done. Crop production may be done better and cheaper with a swarm of small machines than with a few large ones.
One of the advantages of the smaller machines is that they may be more acceptable to the non-farm community. The jobs in agriculture are a drag, dangerous, require intelligence and quick, though highly repetitive decisions hence robots can be rightly substituted with human operator. The higher quality products can be sensed by machines (color, firmness, weight, density, ripeness, size, shape) accurately.
Robots can improve the quality of our lives but there are downsides. The present situation in our country all the agricultural machine is working on manual operation otherwise by petrol engine or tractor is expensive, farmer can’t work for long time manually to avoid this problem, we need to have some kind of power source system to operate the digging machine.
Source: NHCE
Authors: Nithin P V | Shivaprakash S
>> More Wireless Energy Projects for Final Year Students