ABSTRACT
This paper presents a novel and modular approach to agricultural robots. Food production is highly diverse in several aspects. Even farms that grow the same crops may differ in topology, infrastructure, production method, and so on. Modular robots help us adapt to this diversity, as they can quickly be configured for various farm environments.
The robots presented in this paper are hardware modular in the sense that they can be reconfigured to obtain the necessary physical properties to operate in different production systems—such as tunnels, greenhouses and open fields—and their mechanical properties can be adapted to adjust for track width, power requirements, ground clearance, load capacity, and so on.
The robot’s software is generalizing to work with the great variation of robot designs that can be realized by assembling hardware modules in different configurations. The paper presents several novel ideas for agricultural robotics, as well as extensive field trials of several different versions of the Thorvald II platform.
MATERIALS AND METHODS
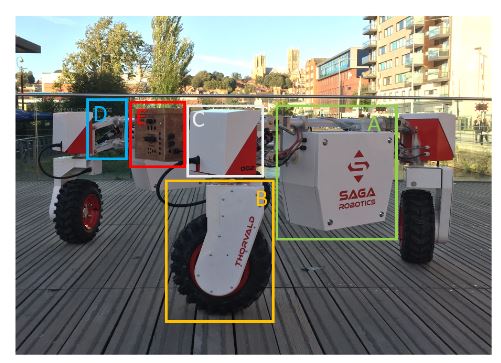
Figure 2. Examples of Thorvald II modules. A: battery enclosure; B: drive module
By default, all battery enclosure modules are designed to serve three other modules with motor power and CAN communication. Battery enclosure modules can be fitted with emergency stop buttons for cutting the contractor on the motor power bus. Resetting a pressed emergency stop button is not enough to restore motor power. For this, the robot must receive a command to reengage the motor bus contractor. An example of a battery enclosure is shown in Figure 2.
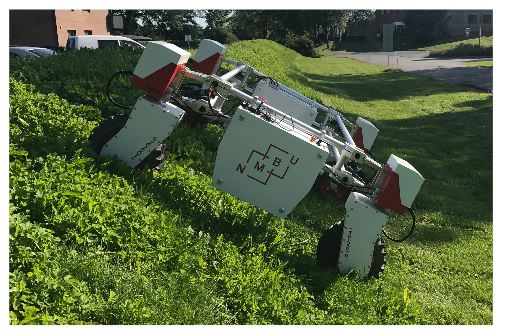
Figure 4. The Thorvald II standard configuration
The standard configuration has been used in various applications, such as robotic harrowing and robotic soil sampling, in several projects and experiments. The robot field capabilities have been verified through many hours of testing in various farm fields and in different weather conditions. The robot is depicted in Figure 4.
RESULTS
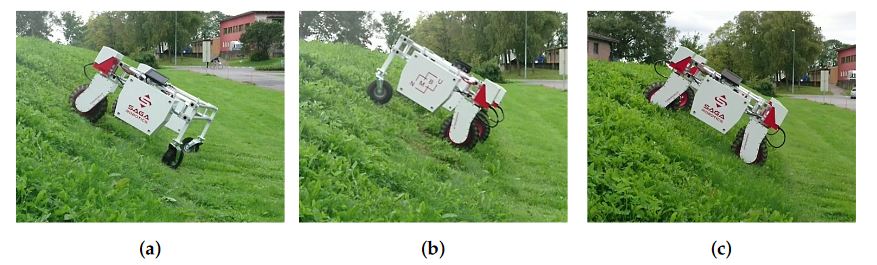
Figure 13. (a) Differential drive configuration failing to climb the incline when drive modules are at the front
With the drive wheels in the front, Configurations 4 and 5 failed at reaching the top as they both lost traction in the middle of the incline. When driving with drive modules at the rear, however, both Configurations 4 and 5 were able to reach the top, from a flying start, descending and starting from rest mid-incline, despite losing traction sporadically. Figure 13 shows some of the robots during testing.
DISCUSSION
As stated above, the presented modules have been used to assemble vastly different robots operating in various environments. In the authors’ experience, the modular system greatly reduces cost and development time related to the creation of new robots. This is especially good for researchers who tend to operate in different environments in different projects, as robots can quickly be adapted for existing farm infrastructure, then later rebuilt to be used in other farms.
CONCLUSIONS
In this paper we have shown how modular robots may be a time saver when it comes to adapting to new environments. The fact that a robot can be modified in-field means that the robot quickly can be altered to adapt to new or changing environment variables. We have shown how robots based on the Thorvald II system are able to operate in several vastly different environments and given examples of current applications.
From the field tests, we learned how flexible frames may be a solution for creating light-weight, low-cost field robots. This is something that will be investigated further in our future work. The work on further developing hardware and software for the Thorvald II system is an ongoing process, and new configurations of the robot will continue to be created as they are needed.
Source: Norwegian University
Authors: Lars Grimstad | Pal Johan