ABSTRACT
FBG sensors offer many advantages, such as a lack of sensitivity to electromagnetic waves, small size, high durability, and high sensitivity. However, their maximum strain measurement range is lower than the yield strain range (about 1.0%) of steel strands when embedded in steel strands. This study proposes a new FBG sensing technique in which an FBG sensor is recoated with polyimide and protected by a polyimide tube in an effort to enhance the maximum strain measurement range of FBG sensors embedded in strands.
The validation test results showed that the proposed FBG sensing technique has a maximum strain measurement range of 1.73% on average, which is 1.73 times higher than the yield strain of the strands. It was confirmed that recoating the FBG sensor with polyimide and protecting the FBG sensor using a polyimide tube could effectively enhance the maximum strain measurement range of FBG sensors embedded in strands.
SEVEN-WIRE STEEL STRAND WITH AN EMBEDDED FBG SENSOR
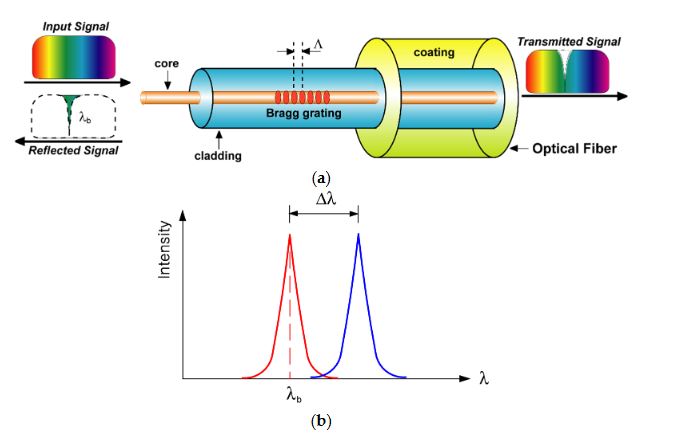
Figure 2. Schematic diagram of an FBG sensor: (a) principle of the FBG sensor; (b) wavelength shift due to deformation by a temperature change or external force
Therefore, the physical quantity can be measured from the relationship between the physical properties and the reflected wavelength of the FBG sensor. Figure 2 shows a schematic diagram of the principle of an FBG sensor. Bragg gratings reflect light at a particular wavelength corresponding to these gratings, while light with other wavelengths is transmitted through the Bragg gratings.
LIMITATIONS AND PERFORMANCE ENHANCEMENTS OF FBG SENSORS EMBEDDED IN SEVEN-WIRE STEEL STRANDS
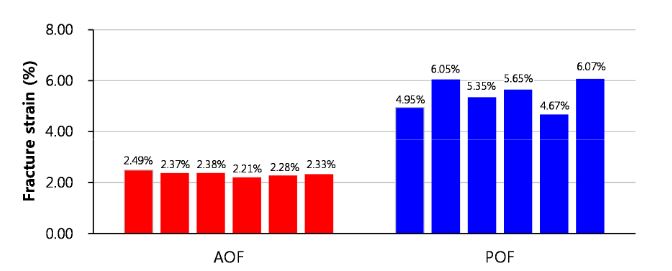
Figure 5. Fracture strains of optical fiber samples
Figure 5 shows the fracture strains of each specimen. The fracture strain of the POF specimens was 2.3 times higher than that of the AOF specimens. From the test results, it was confirmed that the maximum strain measurement range of optical fiber can be improved by the recoating of the optical fiber with polyimide.
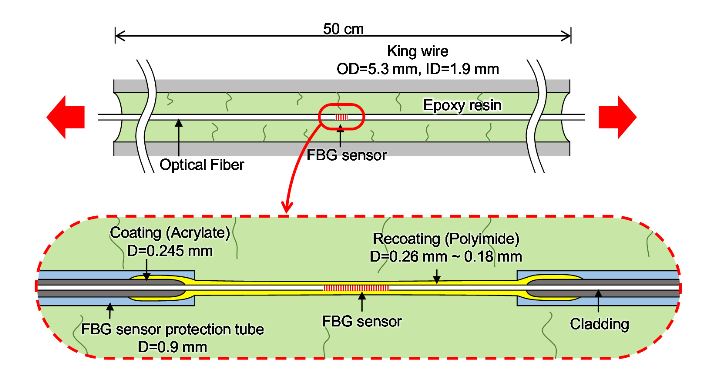
Figure 10. Schematic diagram of the king wire of the smart strand embedding the FBG sensor subject to a tensile load
Figure 10 shows a schematic diagram of the king wire with the FBG sensor subject to a tensile load. Epoxy resin is used to integrate the FBG sensor and the king wire tube in the strand. It was assumed that cracks occur in the epoxy resin, which consequently induces local damage in the optical fiber. This is the main reason for the decrease of the maximum strain measurement range of the optical fiber-based sensor embedded in a strand.
CONCLUSIONS
This study proposed a new FBG sensing technique to enhance the maximum strain measurement range of FBG sensors embedded in strands to measure the strain on the strands in PSC structures. A series of experiments were performed to investigate the effects of recoating materials and of tube used to protect the FBG sensor on the maximum strain measurement range of an FBG sensing system and to assess the validity of the newly proposed FBG sensing system. The following conclusions can be drawn from the current test results:
1. The fracture strain of an optical fiber recoated with acrylate was 0.45%. On the other hand, the fracture strain of an optical fiber recoated with polyimide was 0.79%, which is 75% higher than that of the optical fiber recoated with acrylate. From these test results, it was confirmed that the fracture strain of optical fibers can be increased by recoating the optical fibers with polyimide.
2. The maximum strain measurement range of a normal FBG sensor embedded in a strand was 0.92%. On the other hand, the maximum strain measurement range of the new FBG sensor, which was protected by the polyimide tube, embedded in a strand was 1.73%, which was 88% higher than that of the normal FBG sensor.
Source: Chonnam National University
Authors: Jae-Min Kim | Chul-Min Kim | Song-Yi Choi | Bang Yeon Lee