ABSTRACT
Real-time substructure is a novel hybrid method for the dynamic testing of structures. During an experiment, the structure of interest is divided into two entities. The crucial parts for the project undertaken are physically replicated and loaded dynamically through powerful actuators while the rest is numerically modelled and solved via real-time software.
The dynamics of both substructures must be accurately reproduced, as well as their mutual interaction. The applications are multiple but that of earthquake engineering is primarily considered in this research.
Beyond the accurate modelling of both substructures, three main issues are crucial to the validity of a real-time hybrid simulation. Firstly, the loading equipment must be capable of imposing large loads and accurate displacements on the laboratory specimen.The behaviour of this loading system must be consistent and predictable over a wide range of frequencies and velocities. Secondly, the computational solver employed to emulate the numerical model dynamics requires stability, computational efficiency and accuracy.
It must be able to deal with non-linear multi-degree of freedom systems. Thirdly, the interaction between the two substructures must be reliably emulated by a set of communication devices. The reciprocal boundary conditions must be imposed on the interface of each substructure. This notably implies quasi-instantaneous measurement and application of physical forces and displacements. The two substructures have to be solved simultaneously and in real-time.
The three areas mentioned above have been investigated in this research. Initially, the laboratory installations of the hardware and software were focussed on. The servo-controlled hydraulic actuation system was optimised and a development rig was designed and constructed. It was found that hardware settings could greatly improve the general actuator performance, even though some particular situations could compromise it. This work was then complemented by an extensive study of the necessary actuation compensation.
Numerous algorithms – either previously published or developed in the course of this research – were implemented and formally compared through a set of real-time experiments. Particularly, some challenging multi-axis experiments with a high level of actuator coupling were conducted. Direct extrapolation coupled with adaptive delay estimation was found to be the most effective approach to ensure synchronisation of the substructures. Attention was then given to the integration algorithms used to solve the numerical substructure problem and output the actuator demand on a real-time basis. Both explicit and implicit schemes were considered, even though an explicit formulation is required for this hybrid application.
Computationally simple schemes are more suitable and several were shown to satisfy the necessary accuracy and stability requirements. Successful realtime hybrid tests were carried out with fifty degrees of freedom in the numerical substructure, including non-linear force/displacement relationships and using integration time-steps proving unconditional stability of the algorithms used.
Finally, a realistic earthquake engineering application of the real-time substructure method was conducted. A steel column was tested physically as part of 20-storey building structure subject to the 1940 El Centro earthquake. To further display the usefulness of the method, an energy dissipative device was also integrated in the numerical model and its effect on the building response was shown.
BACKGROUND
This chapter presents a review of relevant previous research. It first assesses the role of RTS as a method of structural dynamics testing. Then, the second section focuses on the integration methods used for solving the numerical substructure model in real-time. The third section focuses on the particular delay limitation imposed by the use of hydraulic actuation and details the various ways this has been directly compensated for so far. The fourth section presents work conducted on control algorithms dedicated to RTS testing applications. Finally, in the light of what is established in the first four sections, the fifth presents more precise challenges for the development of the method.
RTS TESTING IN OXFORD
The structural dynamics laboratory, in which the testing for this thesis took place, is a small laboratory compared with many structural laboratories. It is, however, well equipped. Figure 3.1 gives an overview of the laboratory.
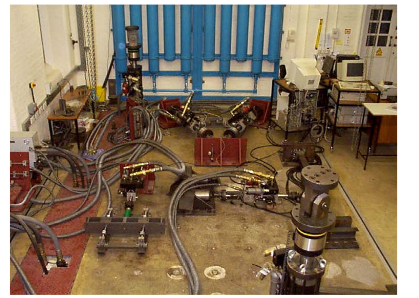
Figure 3.1: Overview of the Oxford University Structural Dynamics Laboratory
THE ISSUE OF ACTUATION QUALITY FOR REAL TIME TESTING
The use of servo-hydraulic actuators is widespread in the field of experimental testing of structures under dynamic loading. Many types of experiments exist, among which cyclic fatigue testing, pseudo-dynamic experiments or large scale real-time shaking table substructure tests can be cited (Williams and Blakeborough, 2001).
Some of these methods use the actuators in an open loop (i.e. the loading history is known before the test is carried out); others require a closed loop and calculate the load signal for the actuator input as the test progresses using a feedback signal and a numerical process. Amongst the closed loop methods, some operate in real-time (Nakashima and Masaoka, 1999) while others are conducted on an elongated time scale (Molina et al. , 2002). The majority of the closed loop tests operate with displacement controlled actuators.
In all of these tests, poor actuation performance (e.g. undershooting, response time, etc.) leads to a lack of accuracy for the measured response. However, in the case of closed loop tests, the lack of accuracy propagates from one loop to the next and is therefore likely to be amplified. For real-time closed loop experiments, poor actuation also often leads to a more severe issue: instability.
ACTUATION COMPENSATION FOR MULTI-AXIS RTS TESTING
The real-time substructure test method is based on splitting the structure of interest into two distinct and complementary entities. There are five main issues to address in order to conduct successful RTS experiments. They can be expressed from the most “physical” to the most “numerical” as follows:
- The level of fidelity for the physical substructure model needs to be high.
- The dynamic actuation hardware and its inner-loop control system need to perform well.
- The outer-loop control problem needs to en sure the boundary conditions at the interface of both substructures are properly applied and measured.
- The level of fidelity for the numerical substructure model needs to be high.
- The computational method employed to solve the numerical substructure in real-time needs to be fast and accurate.
Of all these, points 1 and 4 are crucial “star ting points”, assuming the engineer is able to model the system of interest, partly physic ally and partly numerically. These modelling problems may be complex to deal with but, for this work, they have been respectively avoided and solved by building an arbitrary and simple rig whose properties have been easily measured with adequate instrumentation.
The second point obviously assumes access to some actuation system, able to dynamically apply a load or a displacement. It will be assumed that this equipment is of servo-hydraulic nature, by far the most commonly used type in the field of earthquake engineering. Points 3 and 5 represent, in the view of the author, the main challenges inherent to the RTS method. In other words, these two issues are “created” by the RTS method and are central to its future as a widely available test method for structures under dynamic loading. Point 3 only is of primary interest in this chapter.
COMPARATIVE EVALUATION OF NUMERICAL TIME INTEGRATION SCHEMES FOR REAL-TIME HYBRID TESTING
In Simulink, the model obtained is shown in Figure 6.4. For MDOF systems, this model can accept as its input a vector of deflections that are individually treated to return a vector of restoring forces. The extreme simplicity of the model obtained is of course a great advantage for the real-time applications considered.
The model described here is easy to use with all the schemes presented in details in the previous section, since they are either fully explicit or based on the implementation of an explicit term. In the case of the implicit schemes, the error produced between the explicit term and the exact implicit value obviously also leads to a restoring force error.
REAL-TIME HYBRID EARTHQUAKE SIMULATION OF A STEEL COLUMN IN A 20-STOREY BUILDING
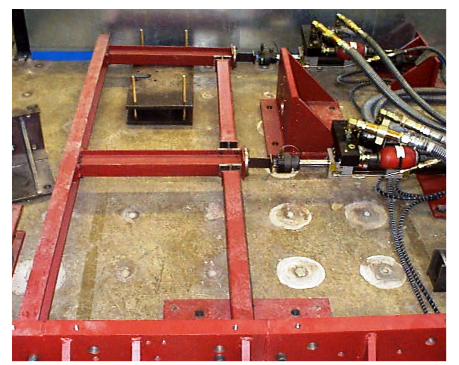
Figure 7.4: Physical substructure laboratory assembly
The test rig is assembled in the OUSDL, as shown on Figure 7.4 with the specimen along the left hand side. Since no major gravity lo ad will affect the behaviour of the physical substructure, the experiment is set up horizontally, at a centre line height of 180mm above the laboratory floor. Note however that a 45mm ball bearing is placed underneath the second storey floor connection beam, rolling onto a platform that can be seen on Figure 7.4. This bearing takes some of the dead weight without introducing any additional kinematic restraint to the setup.
CONCLUSIONS AND FUTURE PROSPECTS
The multi-axis real-time hybrid testing method was developed in this research in relation to its applications to earthquake engineering. A methodical literature review was presented in Chapter 2. Initially, its place and role within the experimental methods of structural dynamics were analysed. The possibilities offered by the RTS method are unique and attractive, and this is illustrated by the fact that other experimental techniques such as shaking table or pseudo-dynamic testing currently evolve towards it.
The challenges posed by RTS were also thoroughly reviewed. The crucial subject of time- integration of the numerical substructure was first assessed. Numerous schemes were presented, some of which had not previously been applied to RTS testing. Their characteristics and relative merits were discussed, as well as their potential suitability for the application to real-time testing of non-linear multi-degree of freedom numerical substructures. This review formed the basis of the comparative analysis carried out in Chapter 6.
The issue of actuator dynamics was then explored and findings from previous literature were summarised. This then led to the presentation of the various compensation algorithms that had typically been used for RTS simulations, based on forward extrapolation and delay estimation techniques. This problem was also analysed more generally with control engineering methods and bespoke adaptive algorithms for substructure testing were presented.
Source: University of Oxford
Author: Paul A. Bonnet
>> Civil Engineering Project Topics using Matlab for Final Year Students with Free Downloads
>> 200+ Matlab Projects based on Control System for Final Year Students