ABSTRACT
While polymeric fabrication processes, including recent advances in additive manufacturing, have revolutionized manufacturing, little work has been done on effective sensing elements compatible with and embedded within polymeric structures. In this paper, we describe the development and evaluation of two important sensing modalities for embedding in polymeric mechatronic and robotic mechanisms: multi-axis flexure joint angle sensing utilizing IR phototransistors, and a small (12 mm), three-axis force sensing via embedded silicon strain gauges with similar performance characteristics as an equally sized metal element based sensor.
PHOTOTRANSISTOR FLEXURE SENSING
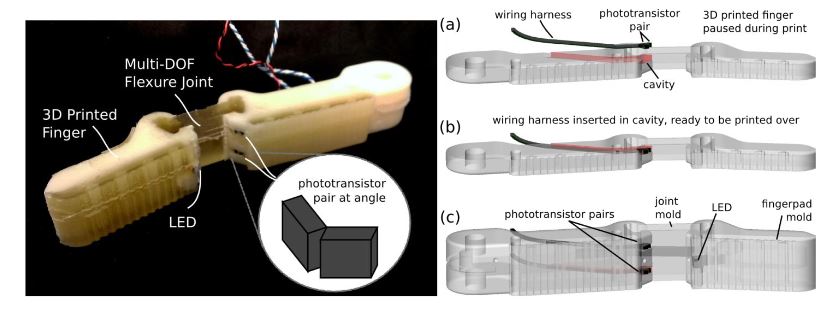
Figure 1. Joint-angle sensor design. An infrared LED shines across the joint onto two angled pairs of phototransistors (left)
The finger design includes cavities for flexure joints (16 mm × 6 mm × 17 mm) and finger pads, which are then filled with two-part urethane rubber (PMC 780, Smooth-On Inc., Easton, PA, USA—Shore-A durometer 80). The walls of the cavities are then peeled off, leaving the flexure joint as shown in Figure 1.
STRAIN-BASED FORCE SENSING
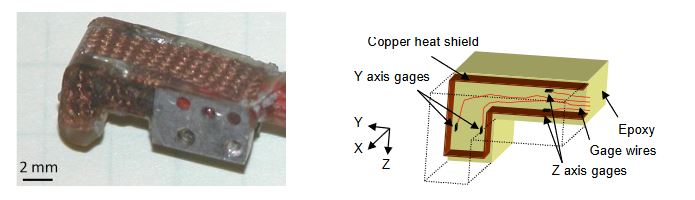
Figure 3. Photograph and cross-sectional diagram of three-axis force sensor. Note copper heat shield
The force sensor is a dual-serial-beam configuration. One strain gauge is located on each of the four sides of the proximal bending beam, sensing two bending moments (corresponding to X and Z forces in Figure 3). Two strain gauges are located in the distal bending beam to sense the final axis (Y) of force (Figure 3). The sensor is integrated with an aluminum base allowing simple attachment to manipulators.
CONCLUSIONS/OUTLOOK
The design approaches and fabrication techniques presented here demonstrate that sophisticated sensors can be readily incorporated into polymeric structures. A central advantage is that the fabrication process can enable the creation of highly effective sensors by embedding inexpensive, prepackaged transducers to create specialized sensing structures. These sensors are part of the robot structure and are created using the same tools and forming techniques as the mechanical structure, requiring minimal additional effort.
This also permits optimization of the overall mechanical properties of the system as well as facilitates cable routing. In the joint-angle sensor presented above, phototransistors and LEDs are molded into a finger during a fused-deposition manufacturing printing operation. This approach is readily extensible to other sensors such as hall-effect sensors and allows easy alignment of the sensors to the device.
In the multi-axis force sensor presented above, the strain gauge wiring is molded within the sensor element, providing strain relief and enhanced robustness. This approach can be applied to the entire robot, with all cabling for sensors and actuators molded into the robot structure. While SDM-like processes were used to fabricate the prototypes presented in this paper, a number of established industrial manufacturing processes exist that can enable similar functionality.
Multi-shot injection molding is used to create parts such as tool handles with integrated soft grips and parts with integral o-rings and gaskets. Overmolding and insert molding allow for the embedding of prefabricated components and are used to encase electronic components within polymer housings. These processes and others might be used directly or slightly modified in order to mass-produce inexpensive commercial polymeric robotic and mechatronic devices incorporating the sensor designs presented here.
Source: Harvard University
Authors: Leif P. Jentoft | Aaron M. Dollar | Christopher R. Wagner | Robert D. Howe