ABSTRACT
The purpose of this study is to computationally model and analyze a Conformable Compressed Natural Gas (CNG) fuel tank for frontal crashes using Finite Element Analysis. Researchers have developed a CNG fuel tank, which is conformable, nonconventional and non-cylindrical. This tank increases cost efficiency, volumetric efficiency and cargo efficiency in CNG vehicle applications.
A lightweight pickup truck (2015 Chevrolet Silverado) has been used to integrate the CNG tanks and field-testing has been conducted to demonstrate the application. The report mainly focuses on the effective finite element modeling of the chassis, brackets and tanks using HYPERMESH and RADIOSS. The frontal crash analysis is simulated according to FMVSS 208 standard for two impact velocities of 35 mph and 55 mph. CAD models of the brackets have been developed for this study.
Material models of the truck chassis and bracket are developed using the available data. An important aspect of this study is to determine an appropriate way to model the CNG tank. The conformable tank’s complex geometry, limitations in the software capabilities and the high computational expenses posed a challenge in this study. An equivalent tank model, having a simpler geometry has been developed and used for this study.
The effective modulus of the equivalent tank was determined by equating the strain energy of the conformable tank to the strain energy of the equivalent tank, both subjected to same loading. The results obtained from the crash analysis conclude that the tanks do not fail in frontal crash and rear crash, and the positioning of the tanks are validated. Recommendation for future work is also provided at the end of this report.
GEOMETRY
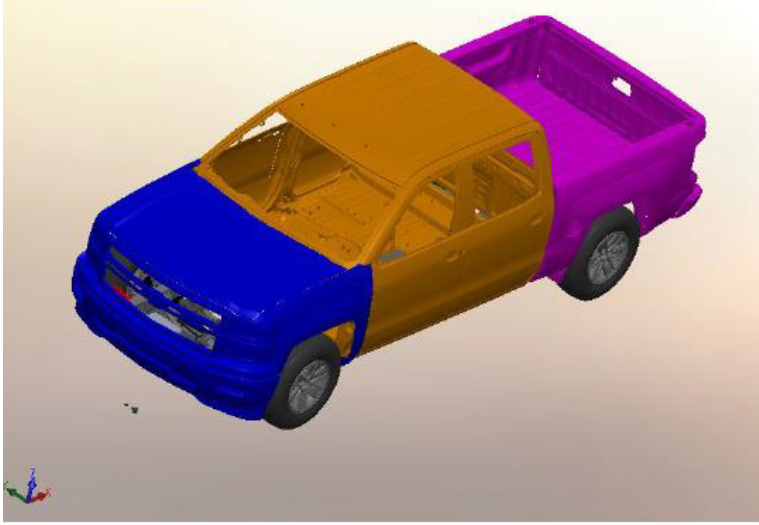
Figure 6- CAD model of 2015 Chevrolet Silverado.
A 3D Computer Aided Design (CAD) model of the pickup truck- 2015 Chevrolet Silverado was received. This CAD file was opened in NX. It was a huge assembly, which had many sub-assemblies like powertrain assembly, chassis assembly, etc. For the project only the chassis CAD was required, so all other assemblies were deleted.
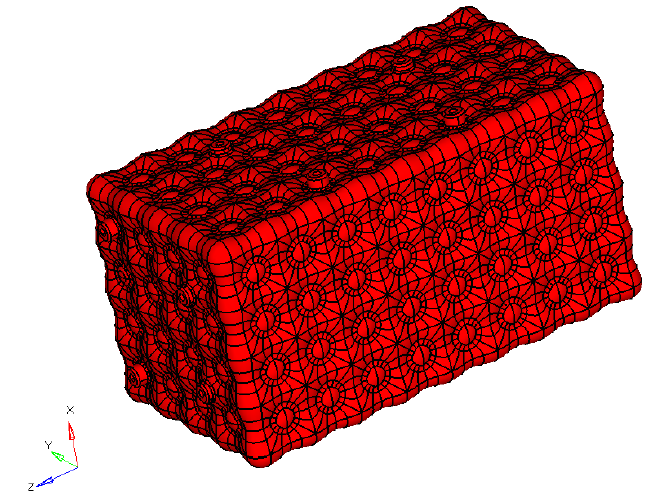
Figure 11-Conformable CNG Tank Geometry.
The tank, designed and developed by REL Inc., has a non-cylindrical tank geometry. The tank is a matrix structure. It has a unique inner structure known as the Schwarz Psurface. They are spherical cells which are packed in an array to eliminate sharp corners. The dimensions of the tank are 22.25 inches × 11.6 inches × 12.24 inches.
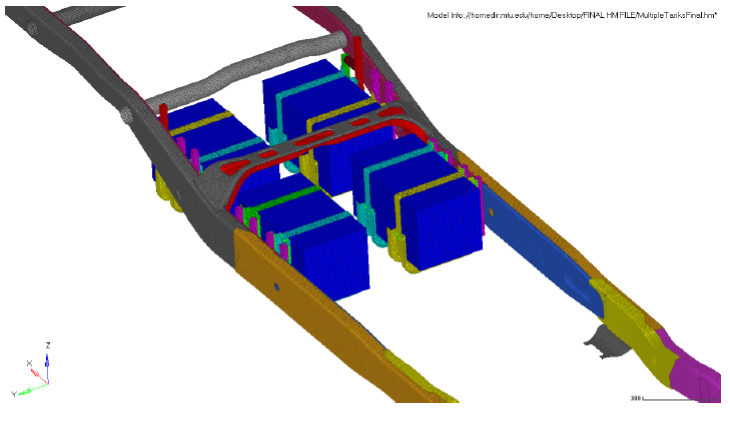
Figure 16- Tanks integrated to the chassis.
After the tank-bracket assembly was created, they were integrated to the chassis. Totally, there are four tanks to be placed on the chassis – two are placed on the left side and two on the right side. The tanks are positioned exactly the same way they are placed in the truck.
MESH GENERATION
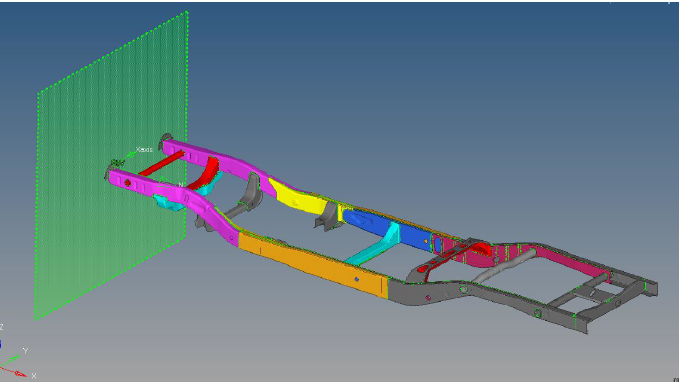
Figure 22-Model for mesh validation of Chassis.
The right element size must be used for meshing, so that the results are not affected by the mesh. This is found out by Mesh Validation study. It is also called Mesh Convergence study. It is important as the mesh convergence study tells us the number of elements required to capture the geometric detail of the part to get the accurate results. Mesh convergence is done by meshing the part by a coarse mesh, and then refining the mesh to a suitable element size.
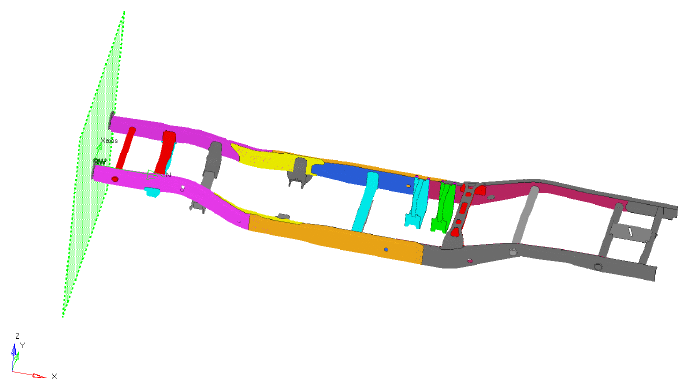
Figure 28-Model for Mesh Validation of Brackets.
Mesh convergence study is very important as it tells us the appropriate element size to be used for meshing in the model so that the results don’t vary significantly. To perform mesh convergence, the loads and the boundary conditions for all models have to be the same. Here the convergence study was performed for 5 element sizes starting from 4mm to 10mm.
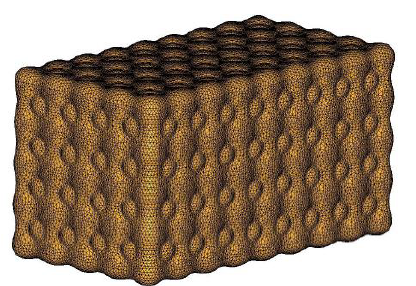
Figure 32-Conformable CNG tank meshed with 3D elements.
The CNG tank was meshed using 3D tetrahedral elements using HyperMesh Solid map mesh command. In the solid map mesh, the user can select a solid, the element length and other quality properties. HyperMesh automatically meshes the part.
MATERIAL PROPERTIES

Figure 36-Symmetric Boundary Conditions applied to the CNG tank.
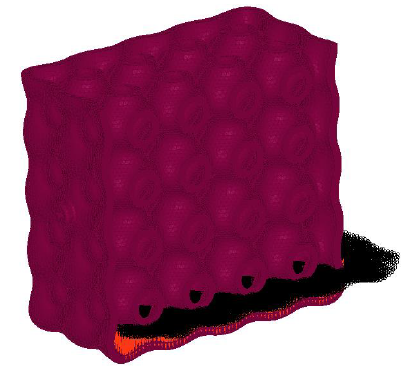
Figure 38-Uniaxial Pressure Load applied to the CNG tank.
As discussed, to simplify the analysis an equivalent tank having a simple geometry is being considered. As the geometry of the proposed equivalent tank and the conformable CNG tank are different, the material properties of AL206 alloy cannot be used. Researches from NASA have proposed a method to develop structure-property relationship of nano-structured materials using equivalent continuum modeling. A similar approach is being followed here to compute the material properties of the tank.
CONTACT MODELING
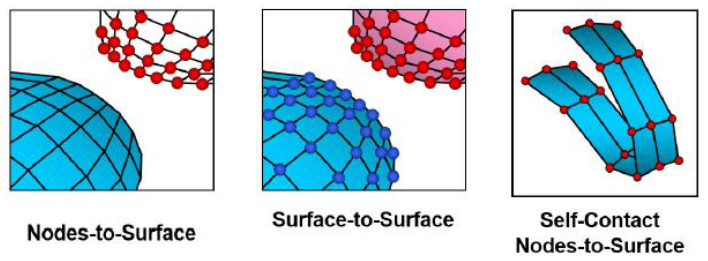
Figure 40-Most common type of Contacts.
Contact modeling or interface modeling is the most crucial part in Dynamic Finite Element Analysis. Contact is the most common source of non-linearity in Dynamic FEA. We know that in FEA the Stiffness matrix (K) is always a function of nodal displacements. In non-linear problems where there is contact the stiffness matrix (K) changes with time. Contact/interface modeling in FEA is where the user defines how parts interact with each other when they come into contact.
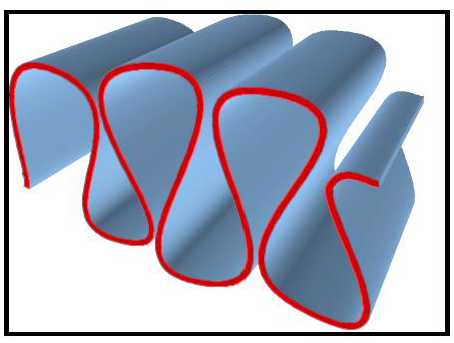
Figure 43-Example of Auto impact surface.
Interface Type 7 in RADIOSS is unique compared to other interfaces as it is non-oriented, i.e. the slave nodes can also lie on the master surface. Due to this reason, this type of contact can be used to simulate auto-impact among all the parts during the crash scenario.
LOADING AND BOUNDARY CONDITIONS
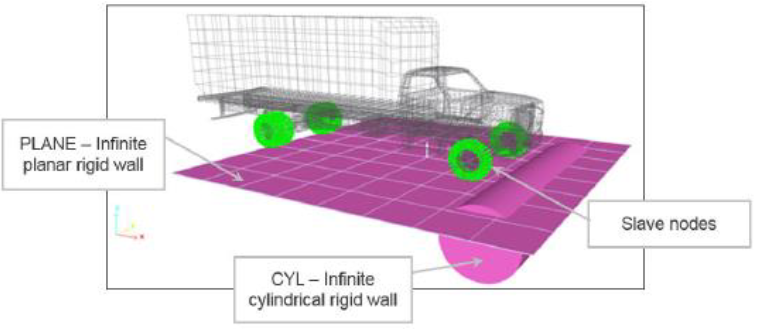
Figure 45-Rigid Wall with slave nodes.
One of the most important and common FMVSS standard used is the FMVSS 208. This is a frontal crash test where the automobile is crashed to a rigid barrier with a fixed speed to check for crash worthiness. For this project a similar scenario is considered, where the chassis is impacted to a rigid barrier (Rigid Wall). The boundary condition here was a rigid barrier.
RESULTS AND DISCUSSION
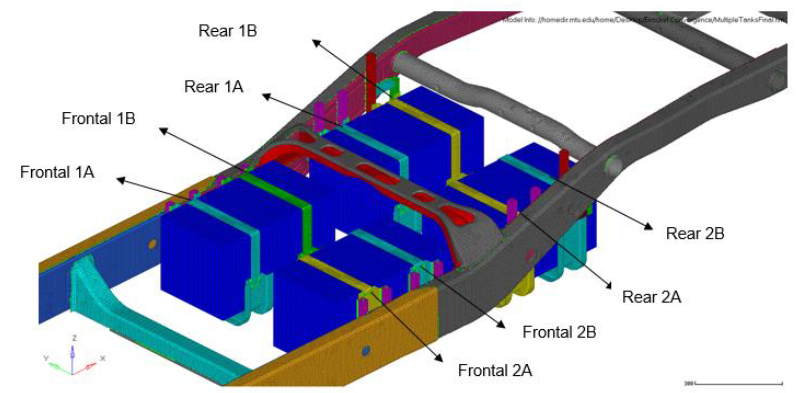
Figure 62-Nomenclature of brackets.
To analyze the brackets, the maximum plastic strain is considered to check if there is any permanent deformation in the bracket. If there in any plastic strain present in the bracket, it means that at that particular location there is a permanent deformation and a possible crack formation. The depth of the permanent deformation decides whether the brackets will break or not. To analyze the results, the brackets are named as Frontal 1A,1B,2A,2B and Rear 1A,1B,2A,2B respectively as shown in Figure 62.
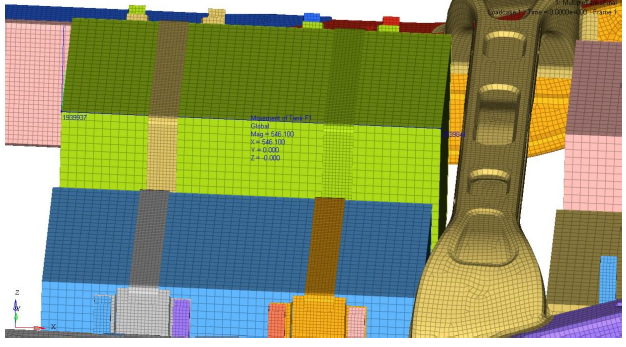
Figure 70- Movement of Tank.
Figure 70 shows the displacement of the tanks due to the rotation of the bracket. The displacement of the tank was found out by measuring the movement of the tank by measuring the displacement of a single edge.
CONCLUSION AND RECOMMENDATIONS FOR FUTURE WORK
The frontal crash analysis of the conformable CNG tank has been performed for two velocities of 35 mph and 55 mph according to FMVSS 208 standard by Finite Element Analysis using HyperMesh/RADIOSS. An equivalent CNG tank has been modelled to replace the non-cylindrical conformable CNG tank. The effective stiffness and yield stress of this tank are computed for the equivalent tank and they are 49.925 GPa compared to 70 GPa of the conformable tank. The yield stress of the effective tank is found out to be 164.25 MPa compared to 350 MPa of the original tank.
The maximum von Mises stress in the tanks for frontal impact are 28.26 MPa (35 mph) and 28.91 Mpa (55 mph), which are way less than the yield stress of the tank (164.25 MPa). The plastic strain in the brackets is zero, which validates the design of the brackets. The maximum movement of the brackets is 1.326 deg (35 mph) and 1.456 deg (55 mph). The maximum movement of the tank is 1.669 mm (35 mph) and 1.794 mm (55 mph).
It can be observed from the maximum von Mises stress on the tanks that the tanks do not fail in frontal or rear crash. The positioning of the tanks is also validated, as the movement of the tanks are so small that they are insignificant. Due to these movements, no other parts near to the tank are affected and this validates the packaging of the tank.
Source: Michigan Technological University
Authors: Datta Sandesh Manjunath