ABSTRACT
Water rocket activities are one of the most popular STEM activities used in primary, secondary, and higher education yet are void of engineering, though engineering is heavily implied in the STEM acronym. This study investigated the amount of engineering present in water rocket activities, and options for emphasizing engineering more in water rocket activities using an open-platform flight simulator for use by educators to enable students to predict flight parameters of a water rocket they designed, and test those predictions against experimental data.
The simulator was constructed in Excel® with many functions, but the function validated in this study was the prediction of maximum height. The simulator was able to predict maximum height of a water rocket at specific input parameters within 5.773% with 95% confidence using a calibration factor to account for unknown sources of error. Further validation of the simulator at other input parameters is needed to ensure the calibration factor enables the accurate prediction of maximum height with varied input parameters, as is common occurrence in STEM water rocket activities.
LITERATURE REVIEW
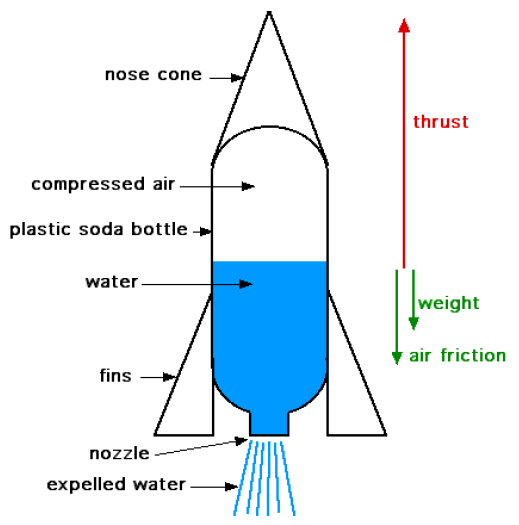
Figure 1. Typical water bottle rocket. (Halliday & Foley, 2016).
The design and construction of the water bottle rocket simply consists of the students constructing the rockets. The students are provided with water bottles, tape, glue guns, cardboard, and/or foam to construct their rockets and are allowed creative freedom (Institute of Electrical and Electronics Engineers, 2016; National Aeronautics and Space Administration, 2016; De Podesta, 2007; Todd, et al., 2007). Figure 1 shows a typical water rocket.
The launch testing phase of water bottle rocket activities consists of launching the rockets using a water bottle rocket launcher, as seen in figure 2, and collecting flight characteristic data using trigonometry, flight duration data, or an altimeter (Institute of Electrical and Electronics Engineers, 2016; National Aeronautics and Space Administration, 2016; De Podesta, 2007; Todd, et al., 2007).
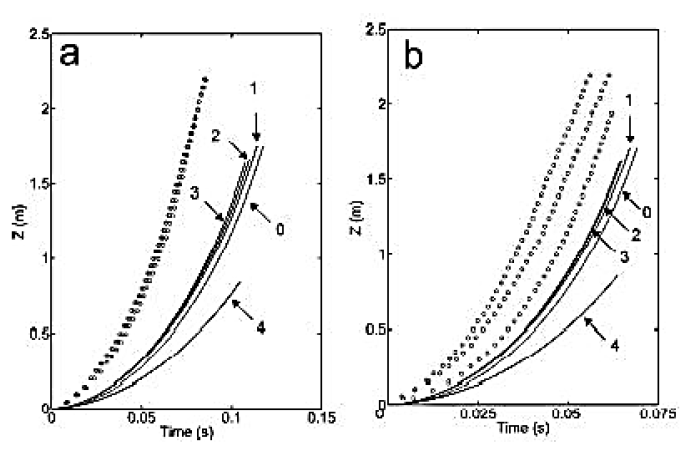
Figure 3. Literature Experimental data compared to theoretical predicted values at (a) 50 psi and (b) 100 psi for rocket height over time. Dotted lines are experimental test data, solid lines are theoretical predicted values (Gommes, 2010).
A particular case is that of Cedric J. Gommes’ study where every known rocket flight phenomena is accounted for including generation of water vapor, transient flow effects, and the real shape of the water bottle rocket and still a large discrepancy between the experimental and the predicted height values appears as is seen in figure 3 (Gommes, 2010).
METHOD
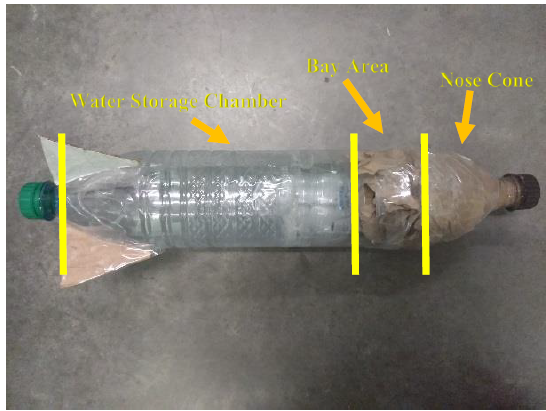
Figure 9. Water bottle test rocket.
Two square foot pieces of paper towel were crumpled and placed toward the nose in the altimeter bay section of the rocket to allow protective cushion for the altimeter during the launch testing to ensure that the altimeter would not fail on impact of the water rocket during testing. A duplicate was also made. The first test rocket was named rocket Alpha (181.9 g), the second rocket made was rocket Beta (216g). Figure 9 shows the water bottle test.
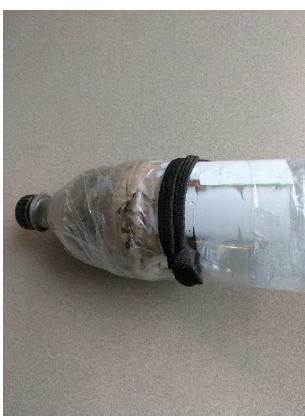
Figure 10. Altimeter Strap Mechanism.
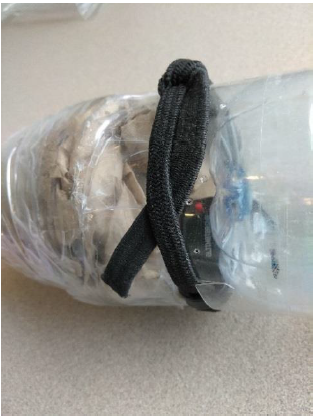
Figure 11. Altimeter Strap Mechanism Close Up.
To launch, first, the altimeter had to be powered on, set to launch mode, and placed inside the altimeter bay of the water rocket. To ensure security of the altimeter in the altimeter bay, a rubber strap was tied to the altimeter and wrapped around the bottle. The strap was assumed to not affect the drag coefficient of the rocket significantly. Figures 10 and 11 show the strap mechanism.
RESULTS
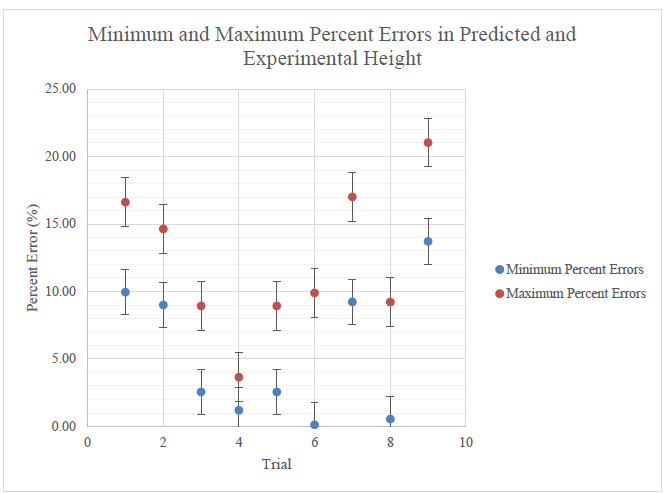
Figure 12. Minimum and maximum percent error in predicted and experimental maximum height for each trial of the first method of launch testing.
Figure 12. Minimum and maximum percent error in predicted and experimental maximum height for each trial of the first method of launch testing. 46ºF dry bulb temperature; 1-3 mph wind speed. Error bars represent the calculated standard error of the data set. The percent error varies more than 20%, which is too much deviation for validating the water rocket simulator.
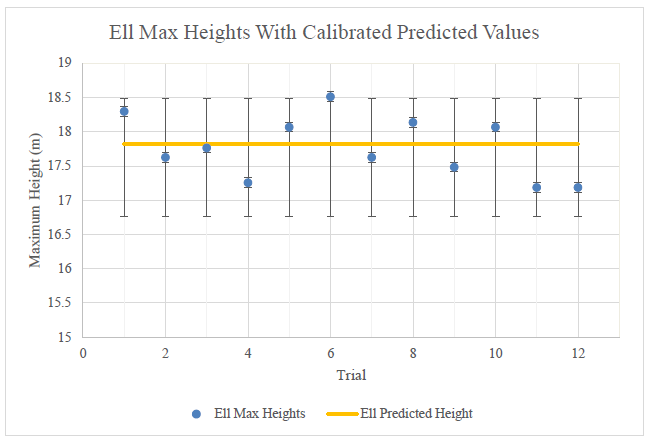
Figure 14. Ellensburg predicted and actual maximum heights.
Figure 14. Ellensburg predicted and actual maximum heights. 23ºF dry bulb temperature; 0 mph wind speed. Error bars indicate the ranges of the data as affected by the precision of the testing equipment. The predicted flight values have an additive calibration factor applied to them of 2.95. The calibration factor was attained by taking the average of the actual calculated heights and then subtracting the original predicted height value.
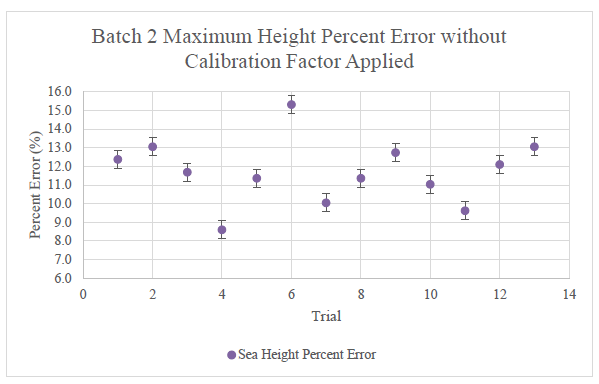
Figure 19: Seattle percent error not adjusted with a calibration factor. The error bars indicate the calculated standard error of just the batch 2 data.
It can be seen from figure 19 that although the standard deviation of the data increased slightly by 8.1%, the mean increased dramatically by 73.1%. This data shows that precision is not the problem, but accuracy is, therefore revealing a flaw in the prediction capabilities of the simulator without a calibration factor.
DISCUSSION
In this chapter, the implications of the results from the second method of launch testing are discussed, including the legitimacy of the results and areas of concern, the generalizability of the results to the use of the water rocket flight simulator in STEM water rocket activities, and further limitations and constraints of the findings. Conclusions and recommendations are also stated. The first grouping of data from the second method of launch testing is discussed first.
CONCLUSION
The study determined that the Excel® Water Rocket Flight Simulator is able to predict maximum height within 5.773% of the actual maximum height of water bottle rockets with 95% confidence. This level of accuracy is only assured with the use of the initial input parameters of 40 psi and 400 mL water volume level in 1 L plastic water bottle rockets. It was not determined if the findings of the study are generalizable to different geometry water bottle rockets or different sets of initial input parameters. However, using the flight simulator and the same initial conditions used in the study will ensure that engineering can be a large part of STEM water rocket activities at the upper division level of STEM education.
By having students predict the maximum height of a water rocket with predetermined input parameters, and then test those predictions against experimental results, the student is able to participate in the practice of engineering and enhance their knowledge of physics and fluid mechanics principles. The student is able to predict a quantitative value, compare that value to an experimental quantitative value, and determine the accuracy of the prediction.
The student will also be able to make suggestions on how to make changes to the original rocket design to ensure that a desired outcome is achieved, i.e. maximum height. They will learn the importance of numerical methods in complex analyses and see how a number of theoretical principles collide in an engineering problem. Therefore, in conclusion, the use of the Excel® Water Rocket Flight Simulator will enable engineering to enter many STEM water rocket activities largely, hence accomplishing the original goal of the study.
Source: Central Washington University
Authors: Melvin Lee Hortman