ABSTRACT
Safety, performance and driving comforts are given high importance while developing modern day cars. All-Wheel Drive vehicles are exactly designed to fulfill such requirements. In modern times, human concern towards depleting fossil fuels and cognizance of ecological issues have led to new innovations in the field of Automotive engineering. One such outcome of the above process is the birth of electrical hybrid vehicles.
The product under investigation is a combination of all wheel drive and hybrid system. A superior fuel economy can be achieved using hybrid system and optimized vehicle dynamic forces are accomplished by torque vectoring action which in turn provides All-Wheel Drive capabilities.
Heat generation is inevitable whenever there is a conversion of energy from one form into another. In this master thesis investigation, a thermal simulation model for the product is built using 1D simulation tool AMESim and validation is done against the vehicle driving test data. AMESim tool was chosen for its proven track record related to vehicle thermal management. The vehicle CAN data are handled in MATLAB. In a nutshell, Simulation model accounts for heat generation sources, oil flow paths, power loss modeling and heat transfer phenomena.
The final simulation model should be able to predict the transient temperature evolution in the rear drive when the speed and torque of motor is supplied as input. This simulation model can efficiently predict temperature patterns at various locations such as casing, motor inner parts as well as coolant at different places. Various driving cases were tried as input including harsh (high torque, low speed) ones. Simulation models like this helps Engineers in trying out new cooling strategies. Flow path optimization, flow rate, convection area, coolant pump controlling etc are the few variables worth mentioning in this regard.
HEAT TRANSFER
Before simulating heat transfer phenomena in an advanced software environment like AMESim. It is very important to learn the basic concepts and mathematical relations beforehand. Advanced softwares should only simplify the job of an engineer but not at the cost of knowing the basic facts.
“In the hands of poorly educated people, these software packages are as dangerous as sophisticated powerful weapons in the hands of poorly trained soldiers” A quote from the book ‘Heat transfer and mass transfer ’ by Yunus A . Cengel (Page 38).
Heat is a form of energy, the science which deals with the rate of transfer of heat from one system to another because of temperature difference is called heat transfer. There are three modes of heat transfer:
- Conduction
- Convection and
- Radiation
All types of heat transfers require the existence of temperature gradient. Of course, energy transfer takes place from a medium at higher temperature to a medium at lower temperature.
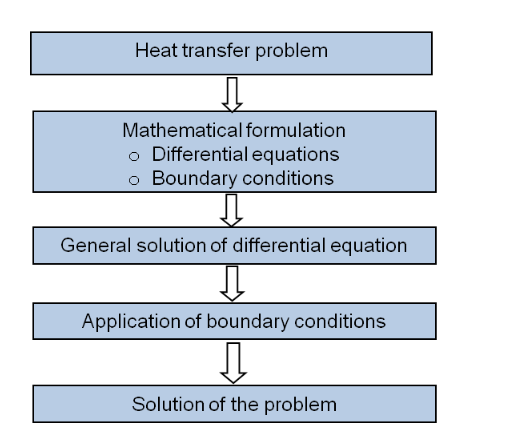
Figure 2.1: General steps in a Heat transfer problem
HYBRID DRIVE COMPONENTS–THEORY
The hybrid drive system is made of electrical and mechanical components. These components are responsible for generation of power, which is then fed to the wheels to drive the vehicle. The components used are not 100% efficient, they produce some losses. The losses are generated in the system as heat. Each components have different parameters that are responsible for heat generation in them. In this chapter, the working as well as the losses generated in the components are explained.
The main components that generate heat in the system are
1. Electric motor.
2. Planetary gears.
3. Bearings.
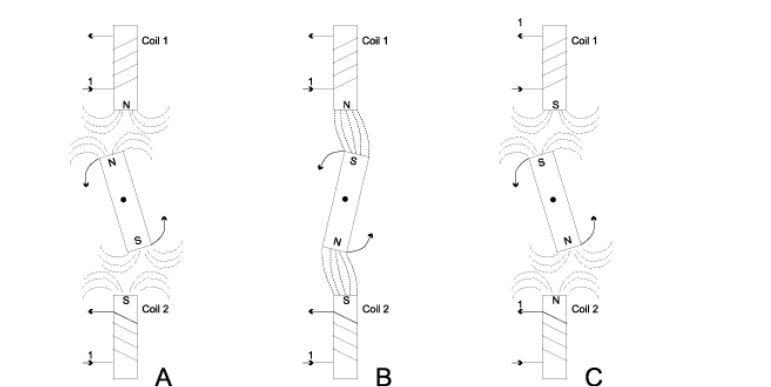
Figure 3.4: Working principle of electric motor
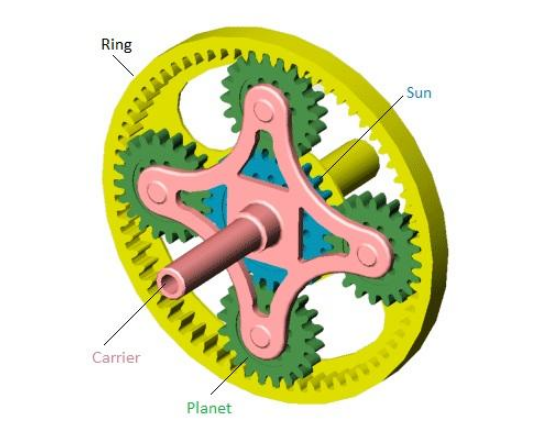
Figure 3.6: Planetary gear train
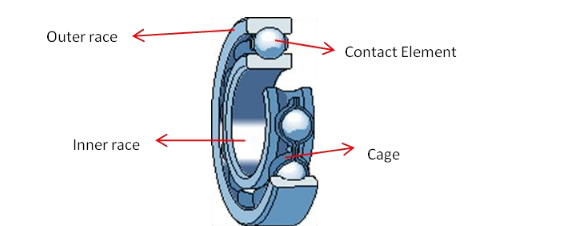
Figure 3.11: Schematics of a Deep grove ball bearing
SYSTEM MODELING IN AMESIM
In this chapter, basic concepts of modeling the system and the approximations made while modeling are explained. The software has built in components in its libraries containing all the components required to design the circuit. The work from the part of the user is to select the right component and input the necessary data. The user guide from AMESim is helpful in understanding and modeling individual parameters in the system. Also some trials were done to understand the sub models better.
Modeling includes sub models from signals and control, thermal hydraulic, thermal and mechanical libraries.
VALIDATION
The simulation model built has to be checked and verified whether it works similar to the actual system or not. This is done by comparing the values for simulation and actual system. Also few other parameters required for the simulation were determined by experiments on the actual system. These details are discussed in this chapter.
RESULTS
This chapter discusses the outcome of temperature variations at various locations in the drive. Temperature readings are compared between the actual drive system and the thermal simulation model.
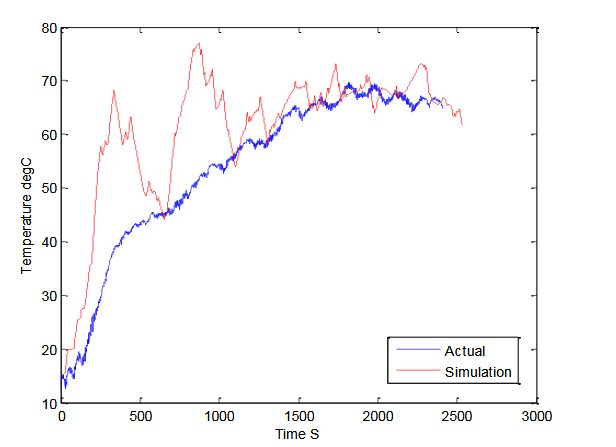
Figure 6.1: Stator winding temperature vs. time
CONCLUSION
The best words to sum up this thesis work and the whole re port is ‘Heat up and cool down’. In retrospect, the problem aroused when the hybrid drive encountered heat generating sources like electric motor and mechanical members such as bearings, gears etc. As demanding conditions were tried out on the drive, the temperature curves kept climbing upwards. Thanks to transfer theories, they were kept below threshold limits.
Simulation model development was done step by step by analyzing problems in pieces. This approach reduces the number variables to keep an eye on, while simulating. When all the heating sources were modeled satisfactorily, they were connected together to form a complete cooling circuit.
This model satisfactorily predicted transient temperature evolution in the drive. Importance was given to radial distribution of temperature i.e. from rotor shaft to drive casing. Thermal contact conductance, convection areas, power losses and coolant flow are the major variables which can make difference to the final result. Some of these variables are hard to figure out , because of the complex nature of heat transfer problems as discussed in the report. CAD models are very important for area calculations.
Convection heat transfer coefficients for complex systems like this are being investigated all around the world, so sensible approximations were made from reliable sources. Simulation results followed the same pattern as the actual ones. So from results section, it can be concluded that the model had around 10% errors in temperature prediction. A ESim helps by reducing Engineer’s effort on mathematics and programming, so that physics of the problem can be thoroughly analyzed.
By keeping this developed model as base, further strategies related to heat management can be formulized. Example cases: coolant pump optimization, changing the coolant, dimensioning the casing for better free and force convection, oil cooling in tank , flow components optimization, etc.
Hopefully, this investigation bolsters the company by reducing the burden of having to produce more prototypes before going into production.
FUTURE WORK
Based on the studies done so far, following works may be investigated in the future:
- Planetary gears (and bearings) can be modeled using available AMESim sub models instead of lumped mass approach as done in this work. Power loss method can be avoided.
- A model including the torque vectoring motor can be simulated.
- New sub models of external surface convection can be created using AMESet or AMECustom and used in simulation.
- A complete secondary circuit with other components can be built, on obtaining the losses values of the other components.
- Distributed mass modeling can be implemented. 6. Some innovative (out of box!) he at management strategies can be tested.
Source: Linköping University
Author: Shiva Kumar B M | kathiravan Ramanujam
>> Matlab Project Topics List with Free Pdf for Mechanical Students
>> Automobile based Matlab Project Topics with Free Base Papers Downloads
>> MATLAB based projects for Mechanical Students
>> Simulation Projects for Engineering Students
>> Heat Energy and Thermodynamics based Projects for Final Year Students
>> More Matlab Projects on Signals and Systems for Engineering Students