ABSTRACT
Devices generating and using non-thermal plasma are often critical parts of industrial set-ups, for purification of exhaust gases. Many research groups work on improvements of plasma generators for ozone (alone or in combination with other oxidants such as H2O2, OH radicals, etc.) production. Such oxidants’ generators can be successfully applied in the case of “point” gas emissions like chimneys of factories or farms and also for “line” emissions caused by road traffic. Presented work describes plasma generator used for the treatment of factory exhaust gas containing hydrocarbons. Data from plasma burn-up of gas from mold painting factory using gliding arc reactor are presented.
GLIDARC REACTOR AND EXPERIMENTAL SET-UP
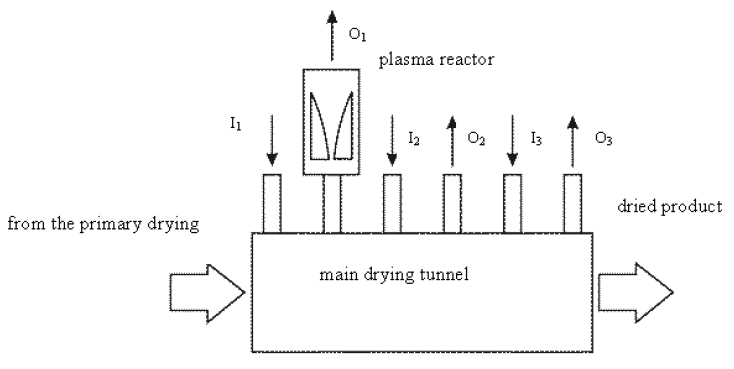
Fig. 1. Schemata of the drying system in the paint shop, (I1, I2, I3)-
hot air inlets, (O1, O2, O3)- polluted air outlets.
Schemata of molds’ drying system with depicted inlets (I), outlets (O) and plasma reactor is presented in Fig. 1. Painted molds were consequently transported via primary drying unit to main drying tunnel, where hot air was dosed through the I1-I3 inlets. Polluted air from the main tunnel was evacuated through the chimneys O1-O3. The pilot plant plasma treatment system was installed on the O1 outlet.
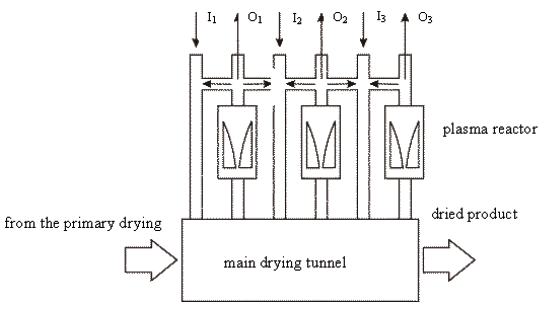
Fig. 2. Schemata of perspective drying system with the hot air recovery.
In the final stage of the project, plasma reactors on all chimneys and PPHARS (post plasma hot air recovery system) are planned. Hot air will be directed back to the main drying tunnel as it is shown in Fig. 2.
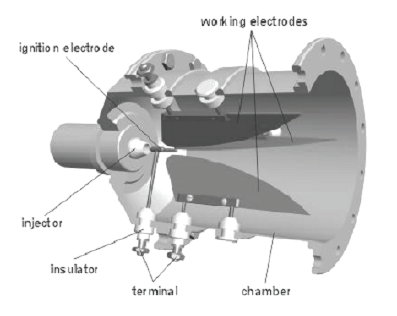
Fig. 3. Gliding arc plasma reactor.
GlidArc plasma reactor construction is presented in Fig. 3. It consisted of one central ingnition electrode and 3 working electrodes placed around the center of the discharge chamber in 120o distance from each other.
EXPERIMENTAL RESULTS
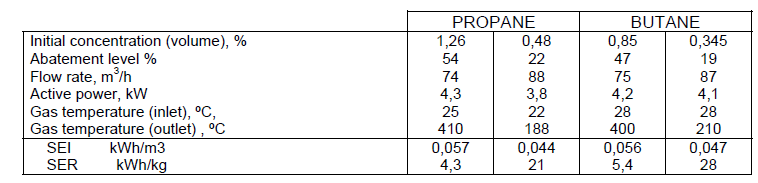
Table 3. Laboratory scale experimental results.
Preliminary tests of the reactor were performed in the laboratory conditions using two substrate gases: propane and butane. They tend to mix with air easily. Moreover, simple chemical structure causes difficulties in their removal if model pollutants are highly diluted in air. Experiments were performed at two different chemical mixtures and two different gas flows with the constant input power. The results of experiments are summarized in Table 3. Indicators SEI and SER depict the usage of electrical energy in the set-up in dependence on the treated gas volume and the mass of pollutants within the treated gas, respectively.
CONCLUSIONS
Pilot installation for paint shop exhaust gas plasma treatment was designed and constructed. Pollutants were partly removed from the exhaust gas stream enabling hot air recovery in the future. The energetic efficiency of the process was considered sufficient and in a good accordance with literature data.
Pollutants’ concentration was much below the ignition level, what assured the safety of applied solution.
No signs of electrodes’ corrosion were noticed during the treatment procedure.
Source: Lublin University
Authors: Joanna Pawłat | Jarosław Diatczyk | Henryka Danuta Stryczewska