ABSTRACT
Damages in composite components of wind turbine blades and large-scale structures can lead to increase in maintenance and repair costs, inoperability, and structural failure. The vast majority of condition assessment of composite structures is conducted by visual inspection and non-destructive evaluation (NDE) techniques. NDE techniques are temporally limited, and may be further impeded by the anisotropy of the composite materials, conductivity of the fibers, and the insulating properties of the matrix.
In previous work, the authors have proposed a novel soft elastomeric capacitor (SEC) sensor for monitoring of large surfaces, applicable to composite materials. This soft capacitor is fabricated using a highly sensitive elastomer sandwiched between electrodes. It transduces strain into changes in capacitance. Here, we present a fabrication method for fabricating the SEC.
Different surface treatment techniques for the nanoparticles are investigated and the effects on the mechanical and the electrical properties of the produced film are studied. Results show that using melt mixing fabrication method was successful at dispersing the nanoparticles without using any surface treatment, including coating the particles with PDMS oil or the use of Si-69 coupling agent. Yet, treating the surface would result in increasing the stiffness of the matrix as well as improving the interaction between the filler particles and the matrix.
INTRODUCTION
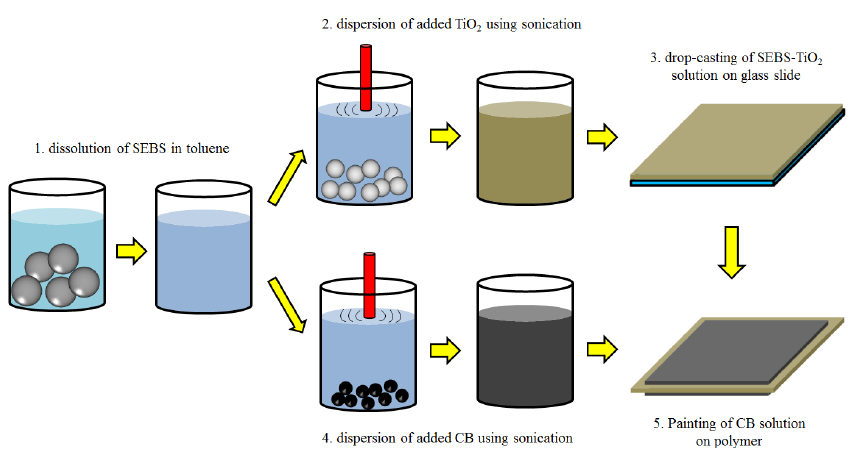
Fig 1: Drop-cast fabrication process.
The original fabrication method for the SEC is the drop-cast (or solution cast) technique. Fig. 1 illustrates the fabrication process of a SEC. The process is initiated by the fabrication of a SEBS/toluene solution. Part of this solution is used to create the nanoparticle mix, in which TiO2 particles are added and dispersed using an ultrasonic dismembrator.
The resulting mix is drop-casted on a glass slide, and dried over 5 days to allow complete evaporation of the solvent. Meanwhile, the remaining SEBS/toluene solution is used to create the compliant electrodes. Here, carbon black (CB) particles are added instead of TiO2 to create a conductive mix. Finally, the CB mix is sprayed or painted on both surfaces of the dried polymer.
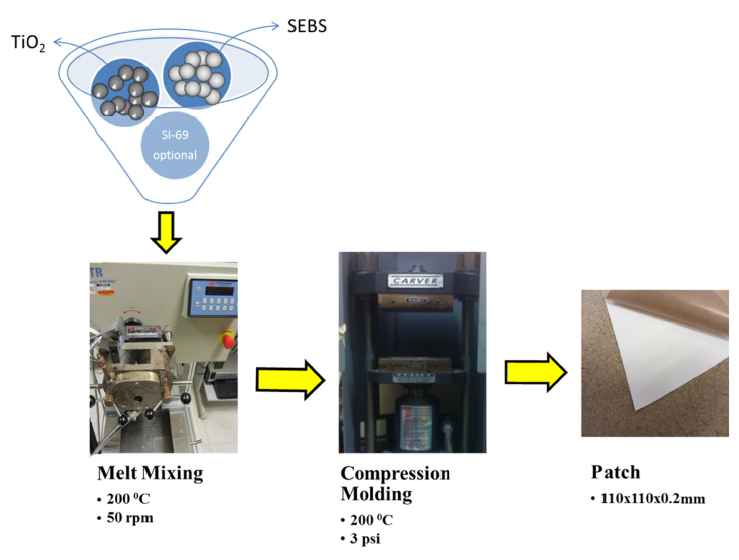
Fig 2: Melt fixing Fabrication Process.
The melt processing technique has been investigated by the authors 14, and research concluded the particle coating should be further investigated to ensure proper dispersion of the nanoparticles within the polymer matrix. The melt mixing fabrication technique is implemented as shown in Fig. 2. The process is done in two steps. First, the polymer and the filler are mixed in a twin-screw heated mixing chamber at 200 °C, 50 rpm.
EXPERIMENT
The samples used for the experiments are listed in Table 1. They are designed to study the influence of chemical modification of the polymer matrix and nanoparticles on the dielectric and mechanical properties. The samples are prepared by blending TiO2 nanoparticles into SEBS by melt mixing with a twin screw internal mixture from C.W. Brabender® Instruments, Inc., NJ. The amount of nano-fillers is adjusted to attain a volume concentration of 15 vol.% in all the samples. Similarly, modified SEBS polymer matrix is prepared by blending 5 ppm of Si-69 into the same twin screw compounder.
RESULTS AND DISCUSSION
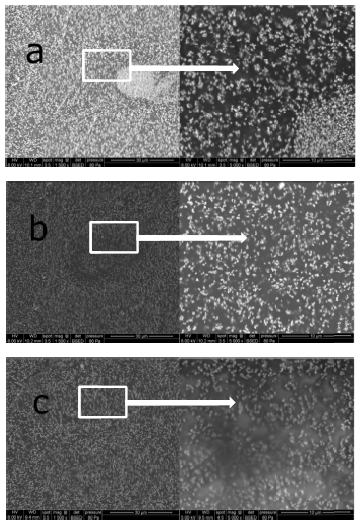
Fig 3. Fracture Surface Morphology of SEBS/TiO2 nanocomposites a) Coated, b) unc, c) uncsi.
A cryo-fracture is created using liquid nitrogen in a randomly selected location for each of the three films with nanoparticles filler. Fig. 3 shows the surfaces at magnification of 1500x and 5000x. The nanoparticles are expected to have a slightly ellipsoidal shape as revealed previously from SEM investigations. They should also exhibit a highly anisotropic static dielectric. Fig.3a to 3c corresponds to the SEM micrographs from cryo-fractured surfaces of investigated samples. The SEM micrographs depict fine dispersion of the nanoparticles in all the samples.
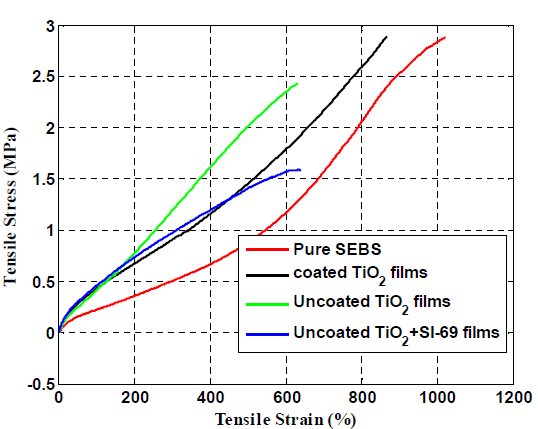
Fig 4. Stress-strain curves the presses films.
Here, the tensile tests for all of the four films are performed. The engineering stress-strain curves are shown in Fig. 4. Young Modulus values are shown in Table. 3. The stress-strain profiles for all the specimens show an elastic response with yield strength less than 0.5 MPa and a high stretching capability before break which exceeded 600% of the original length.
CONCLUSION
Soft nanocomposites made of TPE filled with ceramic particles were prepared to create SEC, for applications to wind turbine blades. We have investigated the melt-mixing fabrication technique for industrial manufacturization of the sensor. The melt-mixing process is seen as an improvement to the drop-cast process, as it has the potential to eliminate the presence of a solvent during the fabrication process.
Two types of surface treatment were investigated to enhance the interaction between the nanoparticles and the polymer particles: 1) PDMS oil; and 2) saline coupling agent Si-69. The results showed that using the melt mixing technique resulted in a good dispersion of the uncoated nanoparticles and treating the surface did not have any significant effect on the dispersion. Conversely, treating the surface enhanced the particle matrix-nanoparticles interaction, resulting in an increase inductility.
Source: Iowa State University
Authors: Husaam S. Saleem | M. Thunga | M. Kollosche | Michael R. Kessler | Simon Laflamme