ABSTRACT
Structural Health Monitoring (SHM) of transportation infrastructures is a complex task, typically conducted by visual inspection due to the technical and economical constrains of existing health monitoring technologies. It results that health monitoring is highly dependent on scheduling and on the judgment of the inspectors, which can be costly and ineffective.
Thus, it is fundamental to automate the SHM process to allow timely inspection, maintenance, and management of transportation infrastructure. The authors propose a flexible membrane that can be deployed over large surfaces, at low cost, for automatic and continuous monitoring of strains. The membrane, termed sensing skin, is constituted by several patches for surface discretization.
Each patch is a soft capacitor, where a measured change in capacitance has a linear correspondence with changes in strain, which allows simple data processing. This paper discusses recent advances in the sensing skin, and demonstrates its promise at smart monitoring of transportation infrastructure. The novel sensor is currently installed on a highway bridge in Ames, Iowa. Preliminary results show the sensor is still functioning as designed. Direct benefits of the proposed technology to transportation infrastructure include 1) improved cost-effectiveness; 2) increased life-span; 3) enhanced resiliency; and 4) higher confidence of the public.
SENSING PRINCIPLE
![Fig. 1. (a) Schematic of Sensing Principle [14]; and (b) a Sensing Patch, 75 x75 mm (3 x 3 in).](http://projectabstracts.com/wp-content/uploads/2017/08/Capture168.png)
Fig. 1. (a) Schematic of Sensing Principle; and (b) a Sensing Patch, 75 x75 mm (3 x 3 in).
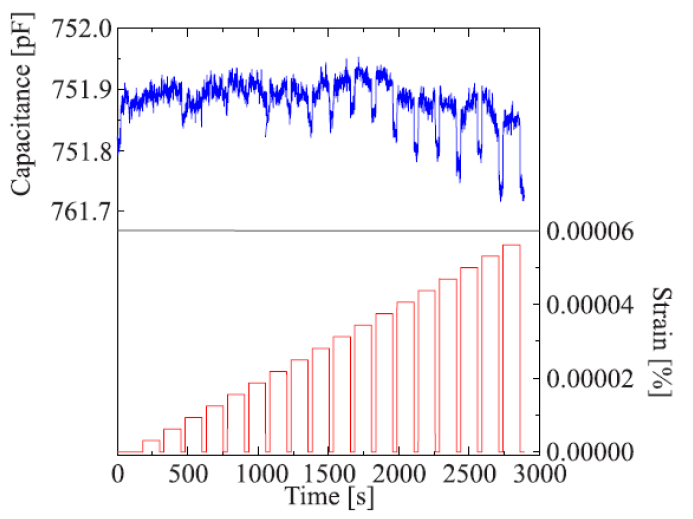
Fig. 2. Capacitance Time History (Above) Under a Quasi-static Strain (Below).
The change in capacitance of a sensing patch under quasi-static strain is shown in Fig. 2. Here, the sensor shown in Fig. 1(b) is pre-strained at 10% and clamped into a tensile tester (Zwick/Roell Z005). Results show that the signal raises well above noise after 0.2 ppm, where 0.1 ppm corresponds to approximately 0.750 μm. Results from Fig. 2 exhibit a drift in the measurements, which could be a consequence of relaxation of the material.
FIELD APPLICATION
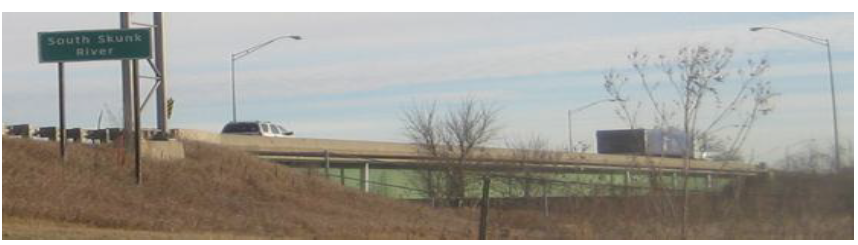
Fig. 3. Skunk River Bridge on the I-30, Ames, IA (Eastbound View).
The structure has been previously used for an SHM project by Lu et al. Fig. 3 is a picture of the bridge (eastbound view), and Fig. 4(b) shows two patches installed under the deck in the longitudinal direction above the first girder from the west side, on which the data acquisition system is located (shown in the bottom right corner of Fig. 4(b)). The installation methodology consisted of sanding the surface, cleaning it with acetone, and adhering the patches using an off-the-shelf epoxy for concrete. The sensing patches were installed in early December 2011.
PRELIMINARY RESULTS
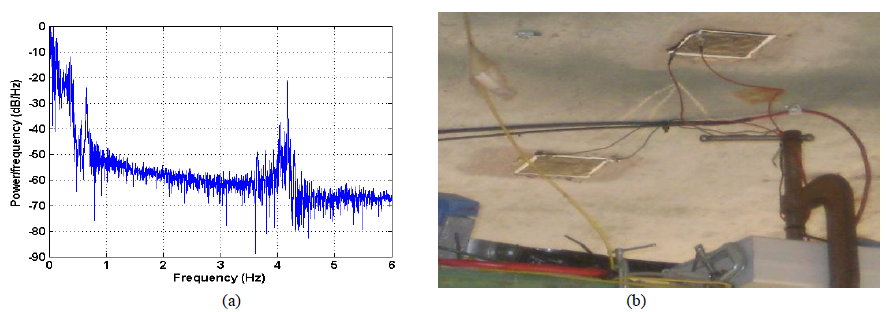
Fig. 4. (a) Power Spectra Density of the Capacitance Signal; and (b) Two Sensing Patches Deployed Under the Deck.
Fig. 4(a) shows the frequency response from the patches obtained on March 18th, 2012. The power spectral density was plotted after minor data cleansing. A principal component analysis (PCA) was performed on the autocorrelation of the signal, and the power spectra density plot obtained from a fast Fourier transform on the reconstructed signal from 68% of the singular values. Results show resonant frequencies at 0.63 Hz and 4.2 Hz.
LABORATORY VERIFICATIONS

Fig. 5. (a) Picture of the Experimental Setup; (b) Pseudo Spectral Density Plot Showing the First Four Frequencies; and (c) Normalized Wavelet Transform of the Response.
Laboratory verifications were conducted to confirm the dynamic sensing capabilities of the patches. Patches were installed on a 5.5 m (18 ft) HP10x42 steel beam simply supported at its extremities, as shown in Fig. 5(a). A chirp signal was generated manually and the patches responses were recorded over approximately 35 seconds sampled at 200 Hz. A plot of the filtered power spectral density is produced in Fig. 5(b). Fig. 5(c) shows a wavelet transform using Morlet wavelets on a section of the original signal extracted using a Tukey windowing function to reduce frequency leakage.
CONCLUSION
We have presented a novel bio-inspired sensor for SHM of transportation infrastructure. Constructed from an array of polymeric capacitors forming soft strain gauges, the membrane allows discretization of strain over large areas, analogous to biological skin.
Preliminary results from the field application on the Skunk River Bridge show the promise of the membrane as a cost-effective SHM solution, and indicate that the sensing material is robust with respect to harsh environmental conditions. Results from laboratory verifications confirmed the dynamic performance of the sensing skin. Impacts of the technology to transportation infrastructure include 1) improved cost-effectiveness; 2) increased life-span; 3) enhanced resiliency; and 4) higher confidence of the public in the installations.
Source: Iowa State University
Authors: Simon Laflamme | Venkata D. Kolipara | Hussam S. Saleem | Randall L. Geiger