ABSTRACT
Structural health monitoring of civil infrastructures is a difficult task, often impeded by the geometrical size of the monitored systems. Recent advances in conducting polymers enabled the fabrication of flexible sensors capable of covering large areas, a possible solution to the monitoring challenge of mesoscale systems. The authors have previously proposed a novel sensor consisting of a soft elastomeric capacitor (SEC) acting as a strain gauge.
Arranged in a network configuration, the SECs have the potential to cover very large surfaces. In this paper, understanding of the proposed sensor is furthered by evaluating its performance at vibration-based monitoring of large-scale structures. The dynamic behavior of the SEC is characterized by subjecting the sensor to a frequency sweep, and detecting vibration modes of a full-scale steel beam.
Results show that the sensor can be used to detect fundamental modes and dynamic input. Also, a network of SECs is used for output-only modal identification of a full-scale concrete beam, and results are benchmarked against off-theshelf accelerometers. The SEC network performs well at estimating both natural frequencies and mode shapes. The resolution of the sensor is currently limited by the available electronics to measure small changes in capacitance, which reduces its accuracy with increasing frequencies in both the time and frequency domain.
BACKGROUND
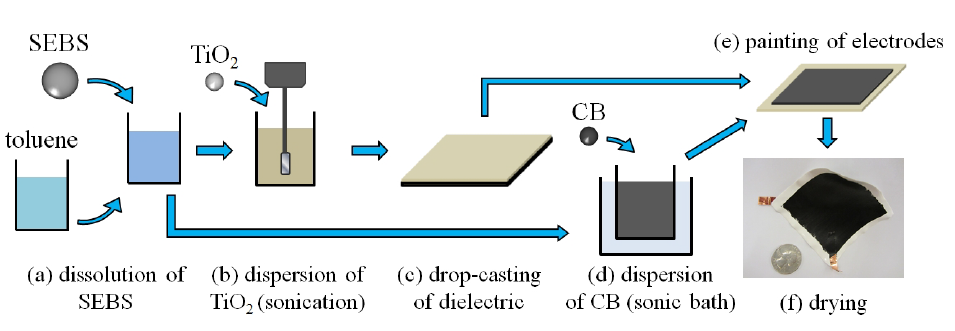
Fig. 1. Fabrication process of an SEC.
An SEC is fabricated using a drop-cast process, shown in Fig. 1. First, the SEBS (Mediprene Dry ex) particles are dissolved in toluene (Fig. 1(a)). The solution is doped with TiO2 rutile (Sachtleben R 320 D) by dispersing a 15% vol. concentration using an ultrasonic tip (Fisher Scienti c D100 Sonic Dismembrator) (Fig. 1(b)).
The SEBS-TiO2 solution is drop casted on an 75 x 75 mm2 glass slides and dries for 48 hours to allow the toluene to evaporate (Fig. 1(c)). While drying occurs, a 10% vol. concentration of CB (Printex XE 2-B) is added to another SEBS-toluene solution. The CB particles are dispersed in a sonic bath over 24 hours (Fig. 1(d)), resulting in a conducting solution. Fig. 1(f) is a picture of a typical SEC resulting from this fabrication 82 process.
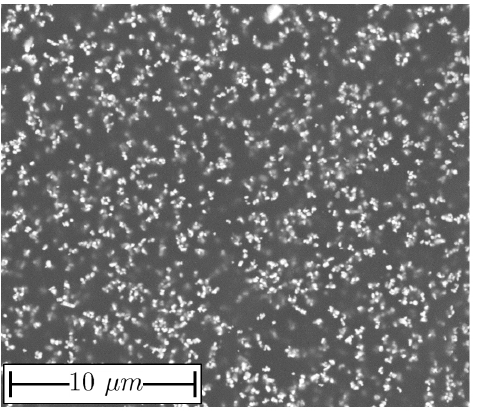
Fig. 2. SEM picture of an SEC.
Fig. 2 is a scanning electron microscope (SEM) picture of an SEC showing a uniform dispersion of the titania particles. It is also possible to use a melt-mixing process to fabricate an SEC, which eliminates the solvents from the process, but further complicates the dispersion of the titania.
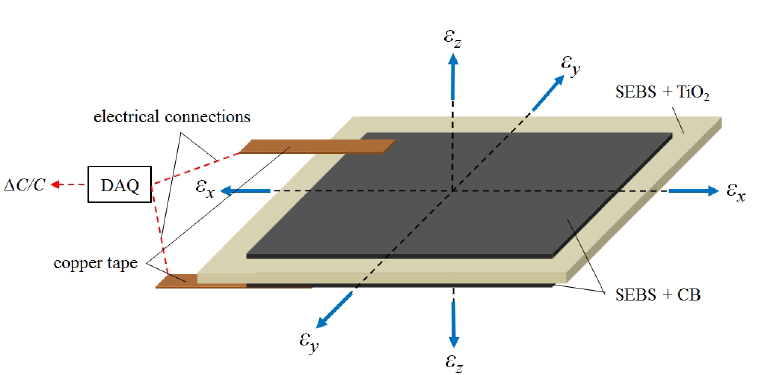
Fig. 3. Sensing principle (layers not scaled).
Fig. 3 illustrates the sensing principle for an SEC wired to a data acquisition system (DAQ), showing 87 the principal strains εx, εy, or εz. A change in strain over the sensing materials is converted into a change 88 in capacitance ΔC which can be directly measured by the DAQ. In monitoring of surface strain, the SEC 89 is adhered onto the surface using an epoxy in the x – y plane, and it is assumed that no external force acts 90 along the vertical axis z. Using Hooke’s Law under plane stress assumption, εz can be written as a function 91 of εx and εy:
DYNAMIC CHARACTERIZATION
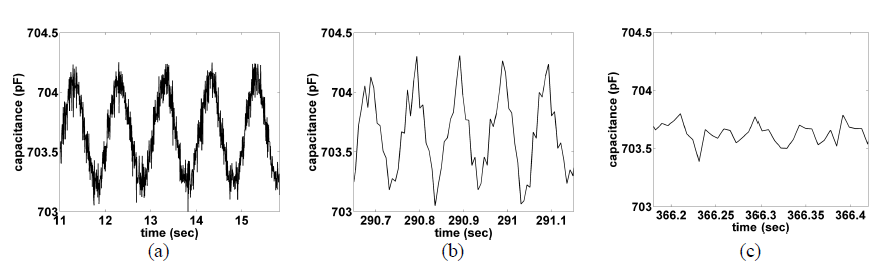
Fig. 5. SEC capacitance signal at (a) 1 Hz; (b) 10 Hz; and (c) 20 Hz.
Fig. 5 is a plot of the 127 typical raw signal from the SEC at 1, 10 and 20 Hz. There is a drift in the signal that can be observed by comparing the average capacitance values between each sub figures. This drift in the signal is linear, and may be caused by the capacitance measurement method from the DAQ. Further investigations on this linear drift will be needed. A comparison between the signals shows that the noise-to-signal ratio increases with increasing frequency.
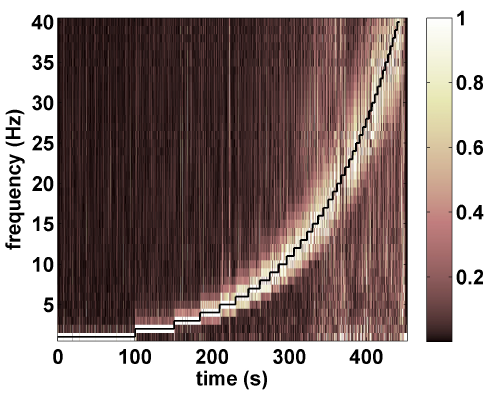
Fig. 6. Normalized wavelet decomposition of the output signal – small scale beam.
This is also observed in the wavelet decomposition shown in Fig. 6. The wavelet transform has been obtained using morlet wavelet, normalized at each discrete time interval to the highest wavelet amplitude. The frequency sweep input, indicated by the black stair-steps line, is clearly identified by the wavelet transform, but the noise-to-signal ratio increases with frequency due to the presence of white noise that becomes significant with respect to the SEC measurements.
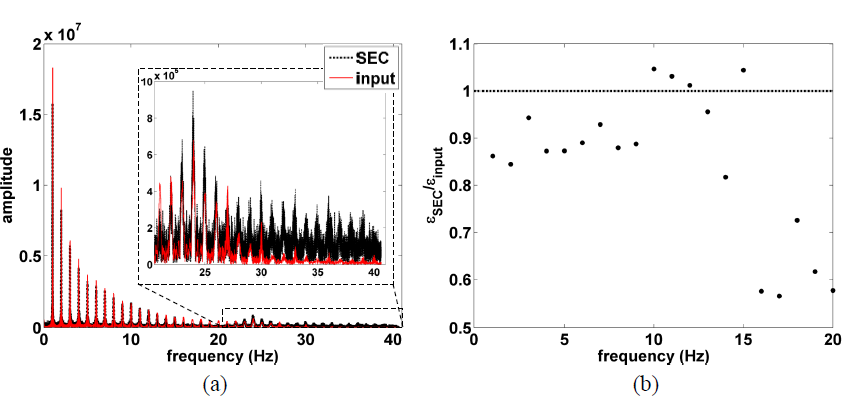
Fig. 8. (a) Fourier transforms of the analytical and measured strain signals; and (b) FRF.
The characterization of the material rheology is out of the scope of this paper. This reduction in peak strain is also observed in the sensor’s frequency response. Fig. 8(b) shows the SEC frequency response function (FRF) plot obtained by dividing the fourier transform of the measured strain by the analytical strain input (Fig. 8(a)), obtained after windowing of the signal using a Tukey window to reduce frequency leakage.
OUTPUT-ONLY MODAL IDENTIFICATION
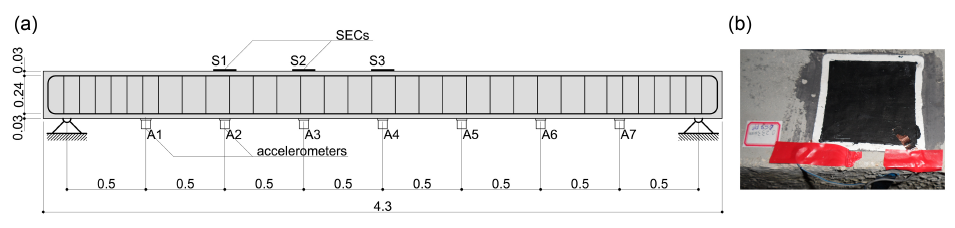
Fig. 12. Experimental setup for tests on RC beam: (a) sensors layout and elevation of the investigated beam (dimensions in inches); and (b) SEC glued onto the beam.
The test consisted of deploying three SECs over a full-scale reinforced concrete beam located inside a laboratory. The tests focused on the range of frequencies from 0 to 200 Hz, covering a wide range of natural frequencies found in typical civil structures. The beam was excited using an impact hammer, and its response measured and recorded simultaneously with the SECs. Results are benchmarked against those obtained through an array of seven equally spaced accelerometers. The layout of the sensors is shown in Fig. 12.
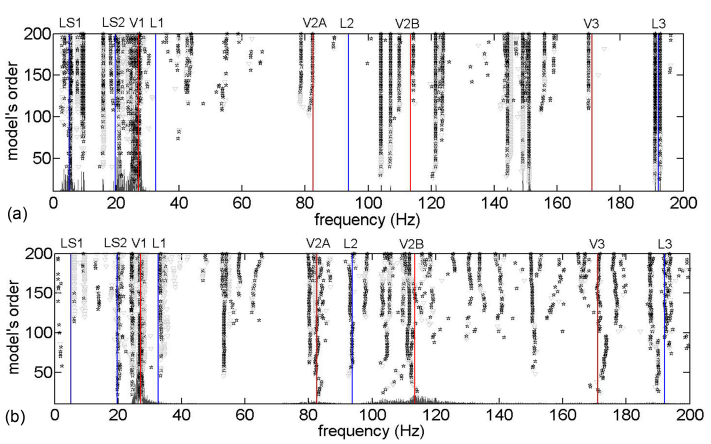
Fig. 13. SDs of SECs ouptuts (a) and accelerometers data (b) (vertical lines denote the modes identified from clustering analysis of the data recorded by all accelerometers).
The SDs of the outputs from the three SECs and three accelerometers placed at the same locations as the SECs are shown in Fig. 13. Consistent poles are denoted by a black star, while a pole that only satisfies frequency and mode shape similarity is denoted by a gray triangle. Modal frequencies identified from clustering analysis are indicated with vertical lines.
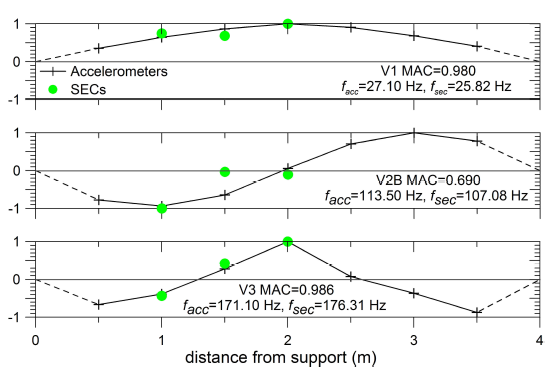
Fig. 14. Mode shapes identified from clustering analysis using SECs and accelerometers.
The mode shapes identified through clustering analysis from the SECs outputs and all accelerometers outputs are compared in Fig. 14. Mode V2A is not shown in these results because it was not clearly identified by the SECs. The other vertical mode shapes identified by the SECs appear to be in good agreement with those of the accelerometers, with high values of the modal assurance criterion (MAC). Larger differences are observed in the second mode (V2B) and can be explained by a lower level of modal excitation and an insuficient resolution of the DAQ.
CONCLUSION
The dynamic behavior of a novel thin film sensor for strain sensing of mesosystems has been characterized. The sensor consists of a thin film polymer fabricated using inexpensive organic and inorganic particles. The particular mix of SEBS and titania constituting the sensor provides mechanical robustness and good sensitivity to strain.
Results show that the sensor was capable of detecting frequency inputs in the range 1-40 Hz, but the presence of noise, likely arising from the DAQ, showed that the SEC was limited below 15 Hz in the time domain. Both full-scale tests conducted on steel and concrete specimens concluded that the sensor was capable of detecting fundamental frequencies up to 200 Hz, comparing well against analytical solutions and-the-shelf accelerometers. A notable feature of the sensor was its capacity to detect modes in any directions, a consequence of the sensor’s bi-directional measurements, which constitutes a great advantage over some of the existing sensing solutions. Lastly, results showed that the SEC could be used in a network configuration to identify mode shapes.
Progress in the electronics has the potential to substantially improve on the sensor’s resolution and accuracy. Given the inexpensive scalability of the proposed sensing solution, along with the bi-directional sensing capability, the SEC constitutes a promising sensor for dynamic monitoring of civil structures by deploying large network of sensors over the monitored surfaces.
Source: Iowa State University
Authors: Simon Laflamme | Filippo Ubertini | Hussam Saleem | Antonella D’Alessandro | Austin R.J. Downey | Halil Ceylan | Annibale L. Materazzi