ABSTRACT
Structural health monitoring of large systems is a complex engineering task due to important practical issues.When dealing with large structures, damage diagnosis, localization, and prognosis necessitate a large number of sensors, which is a nontrivial task due to the lack of scalability of traditional sensing technologies. In order to address this challenge, the authors have recently proposed a novel sensing solution consisting of a low-cost soft elastomeric capacitor that transduces surface strains into measurable changes in capacitance.
This paper demonstrates the potential of this technology for damage detection, localization, and prognosis when utilized in dense network configurations over large surfaces. A wind turbine blade is adopted as a case study, and numerical simulations demonstrate the effectiveness of a data-driven algorithm relying on distributed strain data in evidencing the presence and location of damage, and sequentially ranking its severity.
Numerical results further show that the soft elastomeric capacitor may out perform traditional strain sensors in damage identification as it provides additive strain measurements without any preferential direction. Finally, simulation with reconstruction of measurements from missing or malfunctioning sensors using the concepts of virtual sensors and Kriging demonstrates the robustness of the proposed condition assessment methodology for sparser or malfunctioning grids.
BACKGROUND
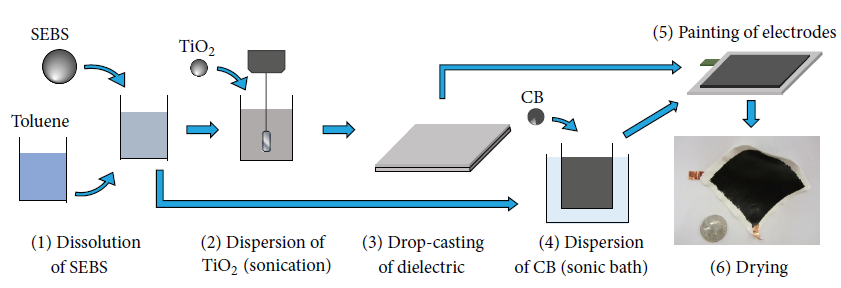
Figure 1: Fabrication process of the SEC.
The fabrication process of the SEC is described in details and illustrated in Figure 1. Briefly, its dielectric is fabricated by dissolving a styrene-coethylene-co-butylene-co-styrene (SEBS) matrix into toluene (Figure 1(step (1))) and incorporating titanium dioxide (TiO2) via sonication to increase the permittivity of the material (Figure 1(step (2))) before drop-casting the solution on a glass plate to allow evaporation of the toluene (Figure 1(step (3))).
While the dielectric is drying, carbon black (CB) particles are added to a solution of SEBS and dispersed in a sonication bath to create a conductive paint (Figure 1(step (4))). Both surfaces of the dielectric are painted with the CB-SEBS solution to create the electrodes and copper tapes are embedded in the paint to create mechanical connections to the wires (Figure 1(step (5))) and allowed to dry (Figure 1(step (6))).
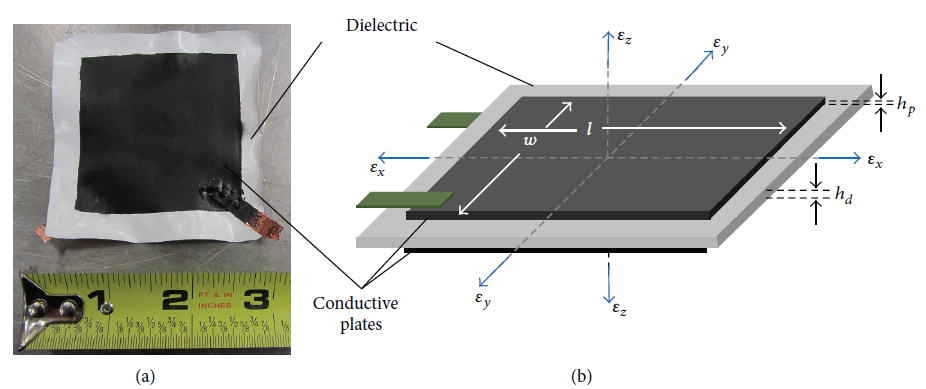
Figure 2: (a) A picture of a single SEC (76.2 × 76.2mm2 (3 × 3 in2)) and (b) schematic of SEC with principal axes.
The SEBS matrix, TiO2, and CB are all relatively inexpensive materials. Combined with the simple fabrication process listed above, the economical feature of the sensing technology highly facilitates its scalability. Figure 2(a) is a picture of a single SEC measuring 76.2 × 76.2mm2 (3 × 3 in2). For small changes in geometry, and considering the reference system depicted in Figure 2(b), where the-axis is normal to the monitored surface can be differentiated to obtain an expression for Δ as a function of the monitored strain.
METHODOLOGY
The capacity of a network of SECs at detecting, localizing, and estimating the severity of damage using the pure signal from is investigated via numerical simulations. This section describes the algorithm used for damage detection and localization, along with the numerical model.
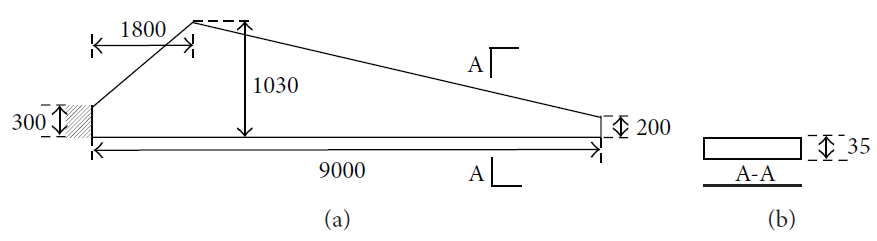
Figure 4:Wind turbine blade dimensions (mm) (a) top view and (b) cross section.
A finite element model of a simplified representation of the CX-100 blade was generated in ANSYS using shell elements. It consists of a tapered cantilever plate of 9m length, 1.03m largest width, and 0.035mthickness, as shown in Figure 4.
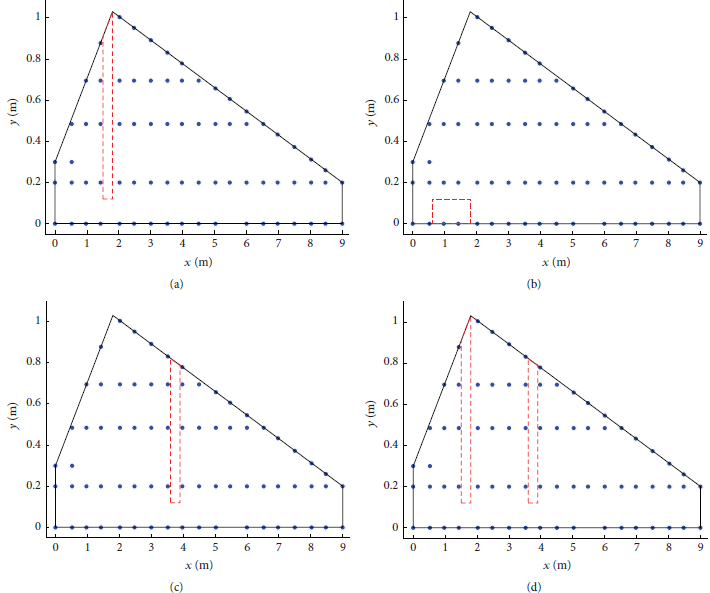
Figure 6: Damage locations under study: (a) location 1, (b) location 2, (c) location 3, and (d) location 4.
Different damage cases are considered in the simulation, consisting of different locations and severities. The four damage locations under study are schematized in Figure 6, represented by the red-dashed parallelograms. The blue circles in the figure represent the location of the simulated 74 sensors.Damage location 1 (Figure 6(a)) is a vertical defect close to the root, damage location 2 (Figure 6(b)) is a horizontal defect close to the root, damage location 3 (Figure 6(c)) is a vertical defect close to mid length, and damage location 4 (Figure 6(d)) is the combination of damage locations 1 and 3.
SIMULATION RESULTS
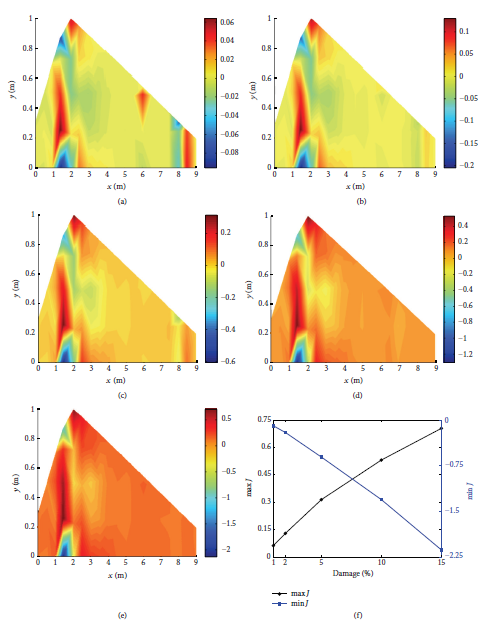
Figure 7: Damage maps for damage cases corresponding to (a) 1%, (b) 2%, (c) 5%, (d) 10%, and (e) 15% reduction in the first natural frequency of the blade.
Figures 7(a)–7(e) are damage maps constructed by computing the relative signal with four closest neighbors and using the undamaged case as the reference relative response map ͞∗. All damage plots were performed by creating triangular elements between sensors and linearly interpolating results between points to create a smoother variation in colors. The damaged area is clearly identified by the darker red region (positive values) for all damage levels.
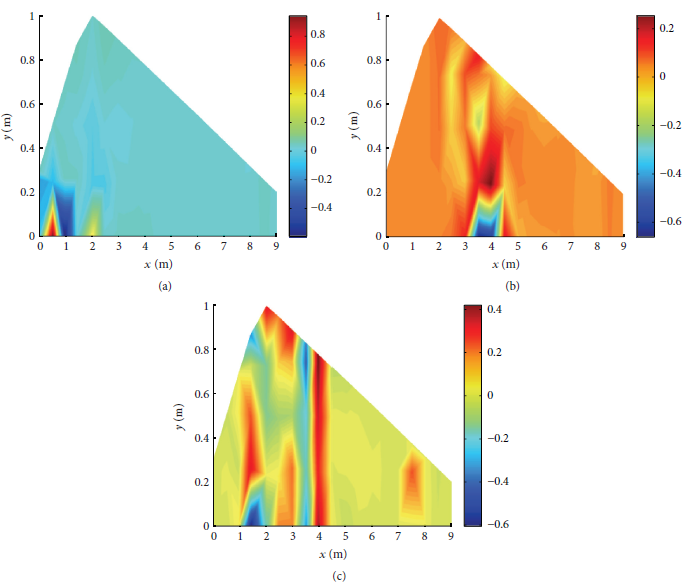
Figure 9: Damage maps for different damage locations: (a) location 2, (b) location 3, and (c) location 4.
Figures 9(a)–9(c) show the damage maps obtained from the SEC network for different damage locations.All simulated damage cases correspond to an approximate loss of 5% in the blade’s first natural frequency.The sensing strategy is successful at localizing all damage.There is a loss in resolution for the joint damage case (location 4). This can be explained by the lower number of sensors located between both damage lines.
SPARSER SENSOR NETWORK VIA KRIGING
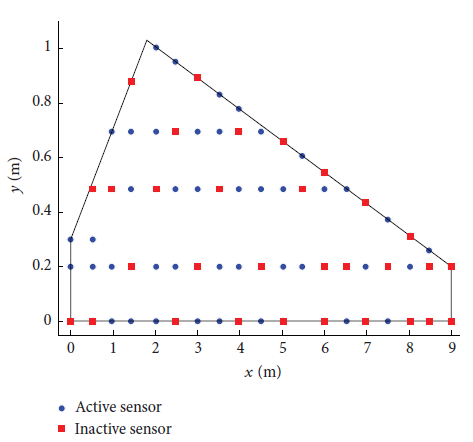
Figure 10: Sparse sensor network under investigation.
This section investigates the possibility of condition assessment from a sparser sensor network that would result from missing sensors or hardware malfunctions, for instance. Additional simulations are conducted by removing 31 sensors, which correspond to 42% of the sensors used in the previous section. Figure 10 shows the distribution of the new sensor network, where the removed sensors are denoted “inactive.”The damage detection, localization, and prognosis exercise is repeated on the different damage levels for damage location 1 using the same wind realization.
CONCLUSION
A strategy for damage detection, localization, and prognosis over large structural surfaces has been proposed. It consists of the deployment of a novel sensor, the soft elastomeric capacitor (SEC), in a network configuration, combined with a simple data-driven algorithm based on raw strain data. Numerical simulations considering a wind turbine blade as the benchmark case study have clearly demonstrated the effectiveness of the proposed structural health monitoring solution in detecting a damage, providing its location, and ranking its severity.
Results have also highlighted that the use of the SEC may provide enhanced damage detection capabilities in comparison with conventional directional strain gauges, because of its additive strain measurement feature. Finally, the application of the concepts of Kriging has strengthened the sensor network approach by replacing missing or malfunctioning sensors by virtual sensors, yet providing a high level of damage detection resolution.The overall performance of the SEC at the condition assessment task, combined with its high scalability, makes the technology a promising candidate for structural health monitoring of large and complex geometries.
Source: Iowa State University
Authors: Simon Laflamme | Liang Cao | Eleni Chatzi | Filippo Ubertini