ABSTRACT
Performance of two different waste heat recovery systems (one based on Rankine cycle and the other one using thermoelectricity) combined with non-hybrid, mild-hybrid and full hybrid systems are investigated.
The vehicle under investigation was a 440 hp Scania truck, loaded by 40 tons. Input data included logged data from a long haulage drive test in Sweden. All systems (waste heat recovery as well as hybrid) are implemented and simulated in Matlab/Simulink.
Almost all systems are modeled using measured data or performance curves provided by one manufacturer. For Rankine system results from another investigation were used. Regardless of practical issues in implementing systems, reduction in fuel consumption for six different combination of waste heat recovery systems and hybrid systems with different degrees of hybridization are calculated.
In general Rankine cycle shows a better performance. However, due to improvements achieved in laboratories, thermoelectricity could also be an option in future. This study focuses on “system” point of view and therefore high precision calculations is not included. However it can be useful in making decisions for further investigations.
SCOPE OF THE WORK IN THIS STUDY
General considerations
This study was conducted at REP (Electric System Development at Scania, Research and Development) as one part of predevelopment studies. The goal was to investigate different combinations of hybrid/mild hybrid trucks associated with waste heat recovery systems, mainly thermoelectric generators. It was required to compare these combinations, via simulations, when they are functioning under different driving conditions. It was also required to compare TEG based waste heat recovery systems with results from Rankine cycle based one.
The fact that the project was conducted at a “predevelopment” stage implies that it was aimed on general perspectives, rather than highly accurate formulations with very well validated results. Hence some simplifications were inevitable to be deployed. However and as a consistent strategy, it was carefully kept in concern to avoid possible oversimplifications and hold an acceptable level of accuracy in the defined scope of the project.
MODEL DESCRIPTION, METHOD AND ASSUMPTIONS
Hybrid Defined Functions
The hybrid system (figure 20) takes care of regenerative braking and the power generated by the WHR. Thirteen switches are used to control the energy flow. Performance map and torque – RPM curves of the electric machine are scaled to the desired power level from Matlab workspace, using a 20 variable.
The inputs to the hybrid model (figure 20) include engine RPM, engine power, braking power, results of TEG model and results from Rankine simulations. In the figure, signal interface between separate blocks within the model is show by arrows. As it is seen electric machine, control unit and battery have two directional interface, which means they send and receive signals to and from each other. System mode is set by RANKINE_STRATEGY (explained below).
In case of a Rankine cycle, the hybrid system also manages the mechanical power in the best way, to be whether converted to electrical power or delivered directly to the crankshaft. This is done via a function box called RANKINE_STRATEGY (figure 21), commanded from the Matlab workspace.
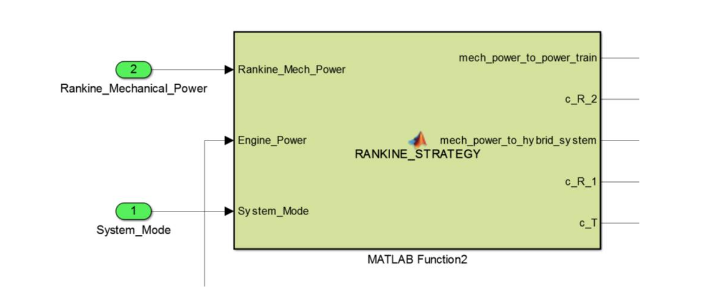
Figure 21. RANKINE_STRATEGY sets the system to function in one of three different modes
TEG System
TEG system A TEG system (figure 25) consists of a set of TEG modules, an extended surface (heat exchanger) at the hot side, a heat exchanger at the cold side (as a part of a cooling system) and a DC – DC converter. There might be a bypass pipe included in the system.
RESULTS AND DISCUSSION
TEG Power Level
To fulfill TEG power requirements of this project, Hi – Z20 modules were used in the simulated TEG system when they are installed following configuration two (section 3.6.2, TEG modules ). After simulating the TEG system (located at outlet of after treatment) over the driving cycle, it was seen that using Hi – Z20 and modified Hi – Z20 modules, it is possible to generate maximum powers equal to 1.1 (named TEGA – ATS), 5 kW (named TEGB – ATS ) with mean values equal to 510 W, 2.25 kW respectively.
It was also seen that if a larger TEG system with improved modules is used a maximum power equal to 10kW (named TEGC – ATS ) with a mean value equal to 3.9kW can be reached. Although, due to large space required for the heat exchanger, the latter system is oversized and does not seem to be realistic, however the results of simulation is presented for comparison reasons. In figure 39 electric power generated by the first TEGA – ATS, when it is placed at outlet of after treatment and simulated using logged data for the driving cycle (Södertälje – Norrköping – Södertälje) is shown.
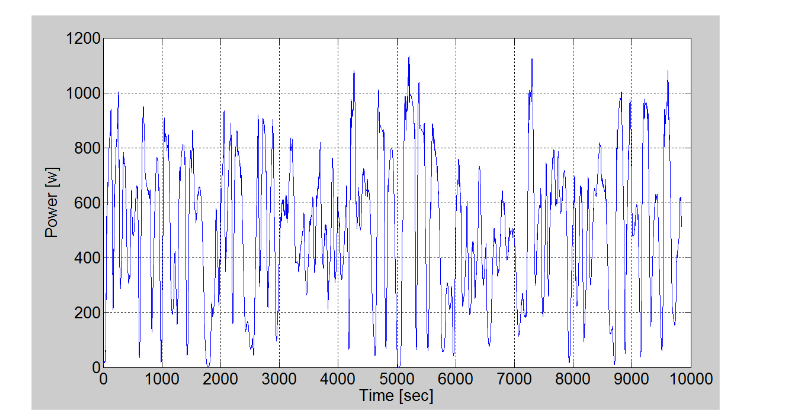
Figure 39. Electric power generated by TEG system (maximum power 1.1kW), when it is located at outlet of after treatment. Driving cycle: Södertälje – Norrköping – Södertälje
CONCLUSION
Results from simulations of all six systems are presented in table 8.
Each of the six different systems investigated in this study, are based on fuel economy viewpoints, implemented in different ways depending on what criterion is the most in concern. Like every other engineering problem, decision is always a compromise between costs and benefits. Results of this study clearly approve complexity of the system under investigation, with a multi – parameter nature. Results of this study (tabel 8) could be used as inputs for economical analysis.
If practical issues regarding to implementation of a Rankine system is resolved, in general it shows more promising short – term future, whether it is implemented in a non – hybrid (3.55%), mild hybrid (4%) or full hybrid system (5.8%). However it should be kept in mind that Rankine cycle holds a long history in industry and it can be considered as a fully developed concept, with apparently no sign of a significant improvement in the overall efficiency. From this perspective special attention should be paid in long – term planning.
TEG system with current technology does not seem to be beneficial (maximum 2%, mostly, 1.5%, from regenerative braking). However TEG system, compared to Rankine system, is easier to be practically implemented. In the meantime there are claims of better performances achieved at laboratories. The present study shows that in short term plans fuel reductions between 1.5 – 3% might be assumed, for mild hybrid or full hybrid systems.
Impact of the storage (battery) is significant (figures 43 to 51), and in close relation with the hybrid power level (figures 52 to 59). A limited power level (say 5 kW), limits the battery’s capacity in such a way number of cells in parallel more than 2 only causes 0.2% fuel reduction (figure 52).
On the other hand, the battery might limit the performance of the system, in a way that increase in hybrid power level does not help any more (figure 53) or even a negative impact due to increased losses in electric machine (figure 54).
FUTURE WORK
Since the present investigation was conducted in a pre – development stage, this study aimed on simulating the system in a general level of simulation precision. It was planned to make simplifications and avoid in detailed engineering calculations for different components. Therefore results can only be used as a road map for future. Nevertheless during the project and while facing different challenges, a list of suggestions was created and completed, as follows:
- More precise model for TEG modules could be made, representing high efficiency modules working at higher temperatures. In order to create these kind of model both mathematical method and using data sheets could be followed. However, in both cases, it is important to combine heat transfer (energy equations) with Seebeck effects (electrical equations) and solve the problem to cover transient behavior of the TEG module.
- A better arrangement of different TEG modules, placed in the heat exchanger could be investigated. TEG modules have different “best performance” working points. Hence placement of Different TEG modules in different stages of heat exchanger might lead to a better overall efficiency.
- An economical analyse for hybrid and also WHR systems give s a clearer picture and paves the path for making final decisions. Investigations include profitability of high rate investing on these systems in compromise with fuel expences as well as polusion reduction necessities.
- The way that thermal energy is extracted from the exhaust gasses could be investigated. Higher ratios of heat flux to back pressure, the temperature at which the heat flux is delivered and also methods to increase efficiency of the heat exchanger might be parts of the investigation.
- A better model for the heat exchanger can be made afterwards.
- Intelligent cooling system might be investigated in order to keep the cold side temperature of TEG modules at its best value, compromising the output power and water pump power requirements.
- More accurate performance maps could be investigated for all hybrid components, to be used in the simulation. Hybrid components include: electric machine, DC – DC and DC – AC converters, inverter, battery and control unit.
- Gathering logged data from driving cycles having power required by auxiliaries excluded from the engine power, might lead to more accurate results from the simulation.
- Simulating the system over different driving cycles, gives better understanding regarding to in which condition what system performs better.
- Investigations regarding to impact of insulating the exhaust pipe, might give a better understanding of more efficient WHR systems, due to increased thermal energy carried by the gasses where WHR is installed.
Source: Linköping University
Author: Mohsen Namakian
>> Automobile based Matlab Project Topics with Free Base Papers Downloads
>> Huge List of Matlab Projects with Free Source Code
>> Matlab Project Topics List with Free Pdf for Mechanical Students
>> MATLAB based projects for Mechanical Students
>> Heat Energy and Thermodynamics based Projects for Final Year Students
>> More Matlab Projects on Signals and Systems for Final Year Students
>> 200+ Matlab Projects based on Control System for Final Year Students