ABSTRACT
This project studies the dynamic response of a composite floor system to excitations from moving fork-lift trucks. The floor system analysed is a system of precast and partially prestressed double-tee elements with a cast in-situ topping.
Currently, there are concerns whether the vibrations caused by fork-lift trucks might exceed acceptable limits due to an ongoing trend towards structures of higher slenderness.This study investigates the mechanical background of the excitation and the current design of the floor system. The study is divided into three major chapters:
Dynamic Fork-Lift Truck Model:
A dynamic load model of a fork-lift truck is developed which can be used in the analytical verification of the vibration serviceability of structures. The model is based on tests performed on four fork-lift trucks in various configurations.The tests are analysed for the spectrum of accelerations. The analysis results in a simple two-degree-of-freedom model. Its only variables are velocity and time. All other values are constant throughout a simulation and depend on the geometry of the specific fork-lift truck and its payload. The frequencies and phase delays are constants and they are verified as Eigen frequencies of a three-degree-of-freedom model.
FE-simulation of Vibrations of a Composite Floor System:
The fork-lift truck model is applied to a three-dimensional model of a composite floor system. The Finite Element model is developed to simulate the construction process of the composite floor system and its influence on the in-service properties of the structure. As part of this work a preliminary investigation of the damping potential of the joint between precast and cast in-situ concrete is undertaken. A linear time-step analysis of the structure is performed and the nodal accelerations are analysed for their magnitude, dependence on the excitation and frequency content.
Field Test:
In order to verify the FE-model of the floor system and the results of the dynamic analysis a field test was undertaken: a floor system was monitored under service conditions. The field data comprise the accelerations of the floor and the forklift truck and the position of the truck relative to the points of measurement. A comparison of the field data and the simulation results proves the validity of both the dynamic fork-lift truck model and the FE-model of the floor system.
DEVELOPMENT OF A DYNAMIC LOAD MODEL FOR A FORK-LIFT TRUCK
This chapter gives an overview of the consideration of loads from fork-lift trucks in the design process and a review of fork-lift truck dynamics in the literature, and explains the development of the dynamic load model of a fork-lift truck. The dynamic load model will be used in finite-element analyses of the vibration response of floor systems to loading from fork-lift trucks and, as such, be a tool for the serviceability check.
The fork-lift truck is analysed as a three-degree-of-freedom system and it is shown that the third mode is unlikely to be relevant for the excitation of low-frequency floors. The model is, therefore, reduced to a two-degree-of-freedom model by ignoring the relative motion between the mast and the body of the truck.
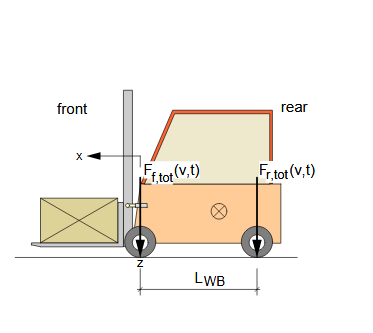
Figure 2.3: 2D model fork-lift truck
NUMERICAL SIMULATIONS OF VIBRATIONS OF A PRECAST AND PARTIALLY PRESTRESSED (SAMPLE) FLOOR SYSTEM
To verify the program SOFiSTiK, a double-tee element was analysed. To simplify the calculation, a simply supported beam was analysed. While the time-dependent effects were incorporated into the FE-model, they were neglected for the verification, because the methods to verify the FE-calculation were not capable to account for these effects. However, the variables of time-dependent effects and their calculation are explained here as well as part of the general description of the FE-model set up.
The geometry of the system is shown in Figure [ 3.1 ] and the main properties are summarised in Table 3.1.
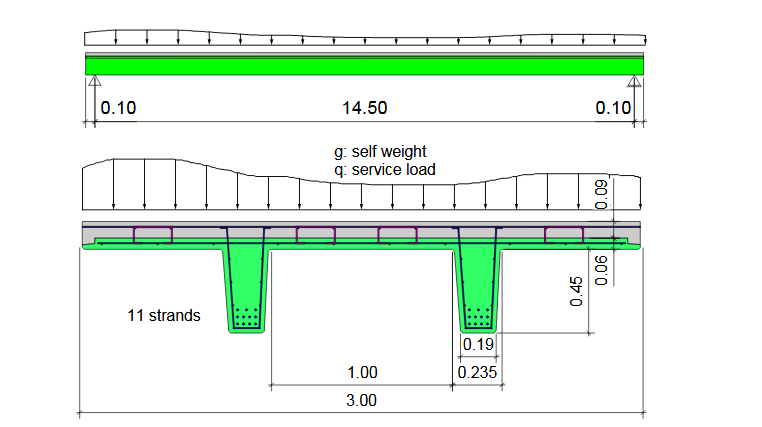
Figure 3.1: System and cross-section of double-tee element
FIELD TEST: DYNAMIC RESPONSE OF THE HELMSTADT FLOOR SYSTEM TO FORK-LIFT TRUCK LOADING
The fork-lift truck available for testing is a Mariotti Mycros 13C, see Figure [ 4.7].
The specifications of this model are summarised in Table 2.5. According to the manufacturer’s data sheet its maximum velocity is 9 km/h (2.5 m/s) without a payload and 7.1 km/h (2.0 m/s) with the maximum payload. This model is significantly slower than the other models tested (maximum velocity ≈ 4 m/s). However, it can be shown that the same load model can be used to set-up the numerical model as for the other models: the natural frequencies, amplitudes of vibration and the relation between velocity and amplitudes are similar to the behaviour observed in the experimental derivation of the load model: see Chapter 2.
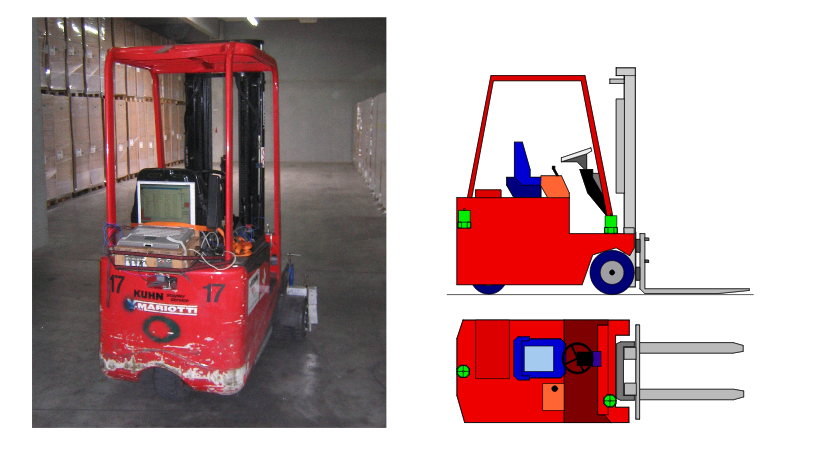
Figure 4.7: Fork-lift truck set up for testing and sketch of positions of accelerometers
CONCLUSIONS
This project aimed to analyse the dynamic response of a precast and partially pre-stressed floor system to fork-lift truck traffic. The aim of developing a realistic and useable assessment methodology for floor vibrations caused by fork-lift truck traffic has been achieved.
The project has been divided into three separate studies. These studies are the development of a dynamic fork-lift truck model (see Chapter 2 ), the development of a FE-model of a composite floor system including all time-dependent effects (see Chapter 3 ), as part of this a preliminary investigation of the joint between the precast and cast in-situ concrete was carried out (see Appendix A ), and a field test to verify the finite element model (see Chapter 4 ). From each study useful conclusions can be drawn.
Source: Oxford University
Author: Andreas Ehland
>> Civil Engineering Project Topics using Matlab for Final Year Students with Free Downloads
>> Top IoT Projects using Matlab for B.E/B.Tech Students