ABSTRACT
We investigate the influence of interfacial treatment on the matrix-filler interaction using a meltmixing process to fabricate robust and highly stretchable dielectrics. Silicone oil and silane coupling agent are studied as possible solutions to enhance the compatibility between the inorganic fillers and polymer matrix. Morphology, thermo-mechanical and dielectric behavior of the prepared specimens are studied.
Results show that specimens filled with silicone oil coated particles have promising dielectric and thermal properties. The mechanical properties reveal a stiffness enhancement by 67% with a high strain at break of 900%. The relative permittivity of the specimens prepared with silicone oil increased by 45% as observed from the dielectric analysis.
EXPERIMENTAL

Figure. 1 (a) Field effect SEM image of rutile TiO2 powder R 320 (b) Crystal structure of TiO2, titanium and oxygen are represented by the larger and smaller balls respectively.
Figure. 1 shows a scanning electron microscopy (SEM) image of R320 powder (a) and its crystal structure (b), showing a distribution of spherical and ellipsoidal shaped particles. Such particles exhibit a highly anisotropic static dielectric. Figure. 1b is a schematic of R320, showing that a high permittivity resulting from the crystalline structure of TiO2. Such structure generates polarization in the material, which increases the dielectric constant.
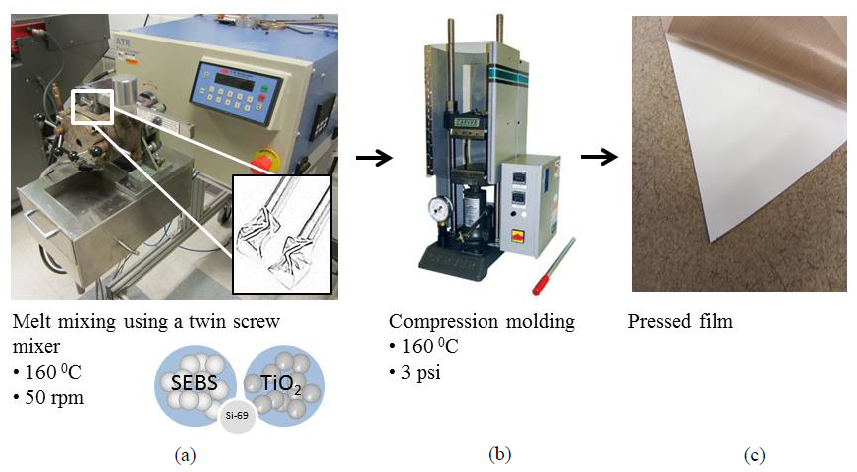
Figure 2. Melt mixing fabrication method: (a) melt mixing, (b) thermal compression molding, (c) final pressed film.
Figure. 2 illustrates the procedure used to prepare the test specimens using melt mixing method. TiO2 was blended with SEBS under constant speed of the twin mixing screws at 50 rpm. The residence time of the melt in the barrel was limited to 10 min to avoid thermal degradation of the melt. The extruded SEBS-TiO2 melt was processed into 200 μm thick films by compression molding at 160oC for 5 min. The sample was left at room temperature to anneal before releasing the pressed plates.
RESULTS AND DISCUSSION
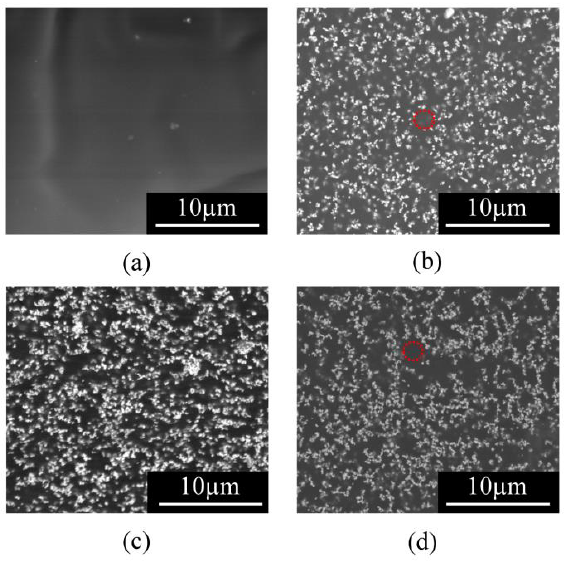
Figure 3. SEM images of a) pure SEBS, b) SEBS-TiO2, c) SEBS-TiO2 (PDMS) and d) SEBS-TiO2 (Si-69). The dotted red circle shows areas with lower density of filler.
Figure. 3a to 3d shows the SEM images from cryo-fractured surfaces of the samples. Images show fine dispersion in all of the samples with fillers. However, the fractured surface morphology of the specimen with PDMS-coated TiO2 particles appears to have a slightly more homogenous structure with fewer gaps. Minor agglomerations are found in the samples with the uncoated filler and the PDMS coated filler. Similar agglomerations are found in composites when the particle-particle interactions dominate the particle-matrix interactions.
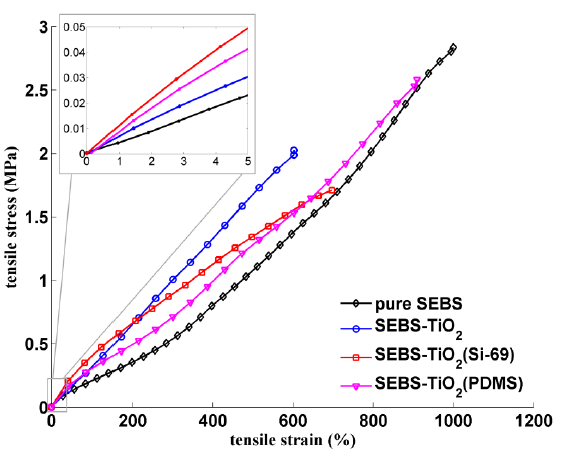
Figure 5. Stress-strain curves of all tested samples.
Young’s modulus measured below 5% strain is listed in Table. 2 and the blow up of this region is shown in Figure. 5. In pure block copolymers, the physical and mechanical properties in the bulk material are primarily governed by their inherent nanostructure. Here the observed difference in the modulus between the four samples can be attributed to the change in the nanostructure present in the post processed samples in presence of nanofillers. Generally, the addition of rigid fillers in soft polymers results in an increase of the modulus.
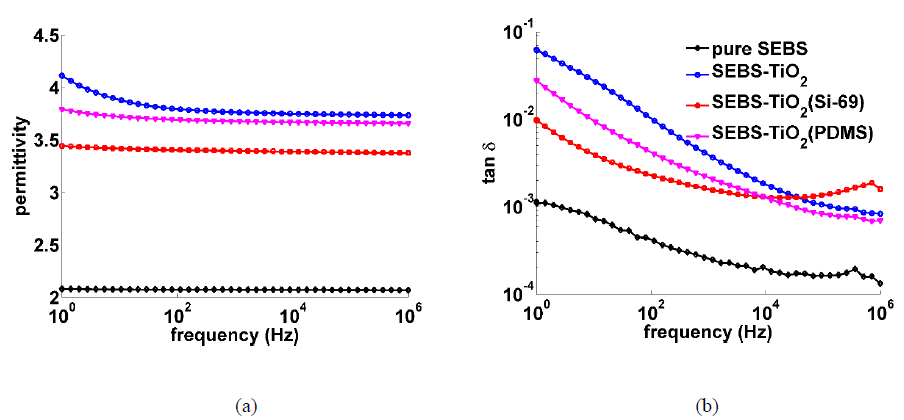
Figure 7. a) Storage modulus recorded at different temperatures, and b) Damping coefficient recorded at different temperatures.
The dielectric relaxation spectroscopy of the pure elastomer and all composites are shown in Figure. 7a and 7b. Results exhibit an increase in the permittivity of specimens with filler content over the whole frequency range. For the pure SEBS, we notice a nearly frequency independent behavior of the permittivity with a value of 2.1 and low dielectric losses. The addition of the TiO2 led to a substantial increase in the permittivity and a significant shift to higher losses. For uncoated TiO2, the permittivity was 3.8 at 100 Hz, approximately twice of the value for pure SEBS, with noticeable frequency dependence below 100 Hz.
CONCLUSION
The interfacial influence of TiO2 and SEBS for melt mixed nanocomposite dielectrics has been studied. Uncoated TiO2 has been compared with surface-treated TiO2, and with a Si-69 enhanced SEBS solution. Morphology, mechanical, thermo-gravimetric, dynamic mechanical and dielectric analyses were conducted on the prepared samples.
The results show that the samples filled with PDMS oil coated particles had superior performance in terms of stiffness where we had 67% increase, stretchability up to 900% before failure and permittivity enhancement by 45% after adding the filler with a small adverse effect observed using the treated filler particles. Moreover, Melt mixing technique used for processing soft, stain sensitive sensors enables producing (soft dielectric with high energy density) sensors with uniform profile properties without involving organic solvent.
Source: Iowa State University
Authors: Hussam Saleem | M. Thunga | M. Kollosche | M. R. Kessler | Simon Laflamme