ABSTRACT:
Granular shoulders need to be maintained on a regular basis because edge ruts and potholes develop, posing a safety hazard to motorists. The successful mitigation of edge-rut issues for granular shoulders would increase safety and reduce the number of procedures currently required to maintain granular shoulders in Iowa.
In addition, better performance of granular shoulders reduces the urgency to pave granular shoulders. Delaying or permanently avoiding paving shoulders where possible allows more flexibility in making investments in the road network.
To stabilize shoulders and reduce the number of maintenance cycles necessary per season, one possible stabilizing agent—acidulated soybean oil soapstock was investigated in this research.
A pilot testing project was conducted for selected problematic shoulders in northern and northeastern Iowa. Soapstock was applied on granular shoulders and monitored during application and pre-and cost-application. Application techniques were documented and the percentage of application success was calculated for each treated shoulder section.
As a result of this research, it was concluded that soybean oil soapstock can be an effective stabilizer for granular shoulders under certain conditions. The researchers also developed draft specifications that could possibly be used to engage a contractor to perform the work using a maintenance-type construction contract.
The documented application techniques from this project could be used as guidance for those who want to apply soapstock for stabilizing granular shoulders but might not be familiar with this technique.
LITERATURE REVIEW
Shoulder Edge Rutting and Edge Drop-Off:
Pavement/shoulder edge drop-off is a critical safety concern for highways and roads that have granular shoulders. “The pavement/shoulder drop-off is created by a difference in elevation between two surfaces of the roadway” (Glennon 2005). When a driver leaves the roadway and encounters the shoulder edge drop-off, the resulting outcome depends on “the driver’s steering and braking response, steer angle, vehicle size, vehicle speed, severity of the vehicle’s departure and return angles, and the magnitude and geometry of the drop-off.”
Shoulder Stabilization:
Soil stabilization can be achieved by either mechanical stabilization or by using a stabilizing agent. So-called mechanical stabilization refers to a process where new aggregate is added to increase the internal friction angle of the granular shoulder material. For granular shoulders, mechanical stabilization could be used to densely grade the aggregate surface, which helps prevent excessive moisture infiltrating the subbase (Hanley-Wood Inc. 1995).
Soybean Oil Soapstock:
Soybean oil soapstock is a biodegradable that shares many of the characteristics of light petroleum-based oil(Skorseth2000). The DUSTLOCK manufacturer claims that it can be used effectively under various conditions (e.g., unpaved roads, driveways, airports, mining sites, parking lots, and construction sites) (EDC 2011a).
PLAN SOAPSTOCK PILOT CONSTRUCTION
Location Selection:
Before the test sections could be constructed, locations needed to be selected for application. Originally, the Iowa DOT was planning to pave shoulders identified with edge-rutting problems around Iowa, but garage supervisors reported many more locations than the budget could address. So, many problematic shoulders could not be paved due to lack of budget.
Pre-Construction Field Tests and Measurements:
On the first set of field trips, researchers brought the printed Google maps for general guidance. After the researchers arrived at the local maintenance garage, the garage supervisor led them to the roblematic shoulder sections and indicated the beginning and end points, at which the 11 researchers marked with wood lath.
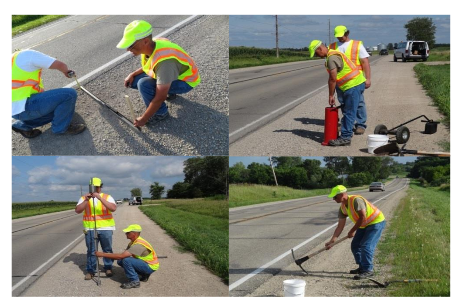
Profile Test(Top Left), Clegg Hammer Test (Top Right), DCP Test(Bottom Left), and Aggregate Samples(Bottom Right).
Equipment Selection:
After the preconstruction observations and tests, researchers began to plan for soapstock application. Some questions had been raised, such as which equipment can be used for application, how should the equipment be arranged for a smooth and safe operation, and what amount of oil and sand will be needed every day? Possible solutions bout the equipment issue were discussed with Iowa DOT personnel and garage supervisors, and the final decisions were made by garage supervisors based on available resources and their previous experience with maintenance operations.
Update of Google Map and New Diagrams:
The map was updated with the start-and end point for each work location marked on a GPS unit during the first trip. By drawing a line that was snapped to the road between the two end points on the map, the length of work was calculated automatically. The amount of soapstock and sand needed were estimated with the calculated length of work and expected spraying width and application rate.
EXECUTE SOAPSTOCK PILOT CONSTRUCTION
Construction activities were conducted at the three test areas selected during the planning stage from August 16 through September 2, 2011. The dates for each area are listed in Table 2.
Application Rate and Overall Productivity:
The water truck ran at a speed of 3 to 5 mph (5to 8 km/hr), which could spray 1/4 gal water over 1 yd2 of shoulder. The soapstock spray rig moved at a speed of 2 to 3 mph (3to 5 km/hr) when spraying soapstock on the moist shoulder with an average application rate of 1/4 gal water over 1 yd2. A sand truck with a chip spreader spread sand on the treated shoulders at a speed of 3 to 5 mph (5-8km/hr), which could achieve an average application rate of 10 lbper yd2.
MONITOR SOAPSTOCK AFTER PILOT CONSTRUCTION
After soapstock was applied on all test sections, post-construction observations and measurements were made to evaluate results. Trips for the full set of measurements and observations were scheduled in late October 2011 and June 2012. Between these official trips, researchers sometimes drove to the field to visually monitor the shoulder performance and obtain updated photos.
Data Analysis:
Percentage of Successful Application Length
During the summer of 2012, researchers visited all test locations to check shoulder conditions to ascertain whether the soapstock application had survived the winter. Researchers measured the length of treated sections with newly -developed edge ruts using a measuring wheel. The error of this measurement was ±0. 6%, which was obtained after averaging the results from 13 measurements for the same 100 ft distance in a flat parking lot.
Research Limitations:
During the construction process, the application rate was not recorded for every shoulder section. The average application rate was taken for several shoulder locations. After the application was made to a few locations, the soapstock spray rig was weighed so the amount of material used could be calculated where actual operation time was recorded.
DATA SYNTHESIS
The research team made observations and measurements during each post-construction field trip. The latest observation was made in late June 2012 (10 months after the initial soapstock application).
Researchers found that most shoulders performed well with soapstock staying firmly on the surface. In a few places, new edge ruts or potholes had developed. In a few other places, soapstock had been removed by traffic although there were no present edge ruts. Results are shown and discussed further for each of the three areas.
Summary Results for All Locations:
Observations were made on 20 treated granular shoulder sections around northern and northeastern Iowa. For each shoulder test section, various tests were conducted to investigate shoulder properties including aggregate gradation, shoulder stiffness, percent grade of the road profile, and cross slope of the shoulder.
In addition, traffic levels were identified using the Iowa DOT database (Iowa DOT 2010). The final percentage of successful applications with regard to length was used as an indicator of the effectiveness of the soapstock application on granular shoulders.
Multiple Regression Model for Rut Mitigation:
Based on the data obtained from the research, the original shoulder properties (shoulder cross slope, CBR, % gravel, and % sand), road traffic volume, and change of rut depth after the application.
SPECIFICATION DEVELOPMENT
A draft specification for the application of soybean soapstock was developed as part of this investigation. The content of the specification was selected for inclusion based on literature review, interviews with subject matter experts, and experience from this and related investigations.
CONCLUSIONS
Most of the shoulders that were tested had good performance in Area I and II where the soapstock stayed firmly on the shoulders after one year’s application. For Area III, the shoulders where the soapstock was applied was not maintained as a soapstock surface after the harvest season of the year in which the soapstock was applied, because the tires of the heavy farm equipment had disrupted the soapstock in many places.
For places where soapstock was observed to work well during the latest observation, a hard crust was formed on shoulder surfaces after the application, and it could support the traffic loads as well as survive from the freezing and thawing process.
There were a few places in Area I and II that soapstock was not applied successfully. In Shell Rock and east of Allison, where rain was encountered during application, shoulder Sections 2.04 and 2.05 had the worst performance with 0% successful application. No edge ruts were observed for these two sections, but none of the soapstock that was applied on shoulder surfaces was visible.
In Garner and south of Algona, shoulder Sections 1.01 and 1.05 experienced small percentages, 1.7% and 4.3%,respectively, of failure. The edge rut in the section near Garner was not severe, (only 0.5 in.deep). There was also one 0.75 in. deep pothole identified east of Waverly and near Denver. Shoulder Sections 2.01 and 2.02 had a few places where soapstock was no longer visible.
The problematic shoulders generally had a strong base, which could support the expected traffic loads, as indicated by average CBRs greater than 12, which is recommended by Mekkawy et al. (2010). The aggregate gradation is generally finer than that specified by the Iowa DOT, as indicated by percentages above the upper fine limit of the Iowa DOT Class A aggregate at #4 sieves.
Most shoulder sections exceeded the I owa DOT specified 4% for cross slope, but there were a few places with shoulder slopes less than 4%, which may increase the potential of water erosion by not allowing water from the shoulder to drain quickly into the ditch.
The application of soapstock took place on 20 test sections over 10 counties of Iowa. The soapstock worked effectively despite situations where aggregate gradation was finer than the originally-specified range for new shoulder material.
The likely causes of failure include rain or saturated moisture conditions during application and high traffic volume (especially heavy farm equipment with luggged tires) during the test period.
For one placethat developed apothole, the failure was corrected with a potholepatcher.The method of application used for this investigation appeared to be adequate. No special techniques or skills beyond those that Iowa DOT maintenance operators normally have were required to run the equipment.
The general application process includes shoulder preparation by conducting maintenance grading shortly before application, spraying water on shoulders to provide anappropriate amount of moisture, applying soapstock on moist shoulders at a 0.25
Source: Iowa State University
Authors: Fangyu Guo | Miguel Andres Guerra | Charles T. Jahren | D avid J. White