ABSTRACT:
GRS abutment systems were studied from October 2010 through December 2011 as a potentially cost-effective and structurally-efficient alternative for supporting LVR bridge abutments.
Problem Statement Iowa currently has approximately 25,000 bridges and about 80 percent of them are on low-volume roads (LVRs). Because many of these bridges are on rural county roads, funding is limited to replace deficient bridges. Performance of substructure components (i.e., abutment and foundation soils) is believed to play a major role in the overall performance of the bridges.
Use of geosynthetic-reinforced soil (GRS) abutment systems, which involves constructing engineered granular backfill material with closely-spaced alternating layers of geosynthetic reinforcement, can potentially be a cost-effective and structurally-efficient alternative for supporting LVR bridge abutments.
However, there are no documented case studies on GRS bridge abutments with performance monitoring information in Iowa. The feasibility of using this method needs to be investigated properly and documented for local conditions and materials with regard to several aspects, including internal and external stability during and after construction, construction methods, and performance monitoring.
PROJECT OBJECTIVES
- Develop an instrumentation and monitoring plan to evaluate performance of newly-constructed GRS bridge abutment systems
- Develop a design approach and construction guidelines for GRS bridge abutment systems with shallow spread footings on LVR bridges
- Document and evaluate the cost and construction aspects associated with construction of GRS bridge abutment systems from detailed field observations on project sites
- Produce a research report and technology transfer materials that provide recommendations for use and potential limitations of GRS bridge abutment systems
RESEARCH METHODOLOGY
A review of literature on GRS abutment systems, material specifications, a newly developed Federal Highway Administration (FHWA)-recommended design methodology and construction considerations, and results from two field demonstration projects are presented in the report.
Bridge 1 – Olympic Avenue:
Bridge 1 involved replacing an existing timber back wall abutment, with a GRS bridge abutment with flexible wrapped geosynthetic and grouted riprap facing , to support a 73 ft RRFC bridge on a reinforced concrete spread footing. No instrumentation or testing was performed by this research team on that project.
Bridge 2 – 250th Street:
Bridge 2 involved replacing a 90+ year-old steel bridge supported on a concrete abutment with a 68.5 ft RRFC bridge supported on reinforced concrete spread footings founded on GRS fill material. The new bridge was longer, so the existing concrete bridge abutments, along with some existing fill, were left in place to serve as GRS facing.
KEY FINDINGS
Savings in Construction Costs:
The construction costs of Bridges 1 and 2 were about $49k and $43k, respectively. These construction costs were about 50 to 60 percent lower than the estimated construction costs for building a conventional bridge with reinforced concrete abutments, piling, and concrete superstructure at these sites.
Laboratory Test Results:
CD triaxial test results showed an increase in effective shear strength parameters when the granular material was reinforced with geosynthetic (Figure 3). Cyclic triaxial test results showed a decrease in total permanent strain at the end of 70,000 cycles when the granular material was reinforced with geosynthetic.
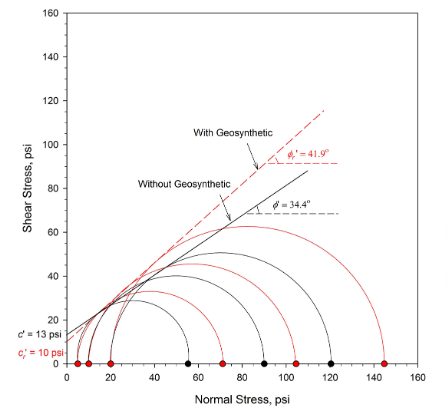
Mohr-coulomb Failure Envelopes From Cd Tests on Granular Materials With and Without Geosynthetic Reinforcement.
Field Test and In-Ground Instrumentation Results:
Bridge 2: Total vertical stress readings in the EPCs located at about 2.2 and 3.8 ft below the footing indicated that the dead load vertical stress applied under the footing (about 2,120 lbs/ft2) was almost fully transferred down to the bottom of the GRS fill material. The horizontal dead load stresses along the excavation walls were about 600 lbs/ft2 or less. The horizontal to vertical stress was less than 0.25, thus indicating low lateral stress on the soil surrounding the GRS fill material.
Bearing Capacity and Slope Stability Analysis Results –Bridge 2:
Bearing capacity analysis was conducted for three potential failure modes: A – bearing capacity failure within the foundation soil, B – bearing capacity failure within the GRS fill material, and C – punching shear failure through the GRS fill material and bearing capacity failure in the foundation soil.
IMPLEMENTATION BENEFITS
The primary benefits of using GRS bridge abutments for low volume road bridges include (1) cost savings due to lower material costs than conventional reinforced concrete bridge abutments and piling, less need for highly skilled labor, and less construction time; (2) ease in construction; and (3) less disruption to traffic due to short construction times.
IMPLEMENTATION READINESS
GRS bridge abutments were constructed using existing abutment wall and grouted riprap as facing elements in this research study. In situ test results from the two demonstration projects in this study indicated that the bridges performed well within the monitoring phase of the project. Performance of these structures over a long period must be investigated. Long-term performance of GRS abutments with different facing elements (e.g., sheet piles, concrete masonry units, and timber-faced walls), must be evaluated.
Source: Iowa State University
Authors: David J. White | Pavana K. R. Vennapusa | F. Wayne Klaiber